Process
Concept
The initial concept begins with an idea, either inspiration or commission. When a client commissions Anthony, they will discuss the purpose and scope of the project. Everything from the narrative of the piece, inspiration, feel, look, pose, time-line, and budget. After an estimated budget is established, a timeline is mapped out with key stages and the deadline. A drawing or maquette is created to visually navigate the idea and to discuss the design. Once the design is approved by the client, the next phase of the journey can begin.
Sculpting
Anthony works from a live model. This is always the ideal approach to capturing the life of the subject. However, Anthony understands that this is not always possible. Sometimes the subject’s time is demanded elsewhere. In these cases, he can still capture a remarkable likeness through photography and reference materials.
Anthony begins the sculpting phase by creating an armature to support the clay. He then works over a series of sessions to create the finished piece. Every sculpture is different and so projects will vary based on size, complexity and overall goals. The sculpture could be completed in as little as a few sessions, or it could take several weeks or months. Once the clay model is near completion, Anthony will ensure that the client has the opportunity to view the sculpture and request alterations. After Anthony completes any alterations proposed by the client, he ensures that the client approves the model before moving to the next phase. (Click images to see process)
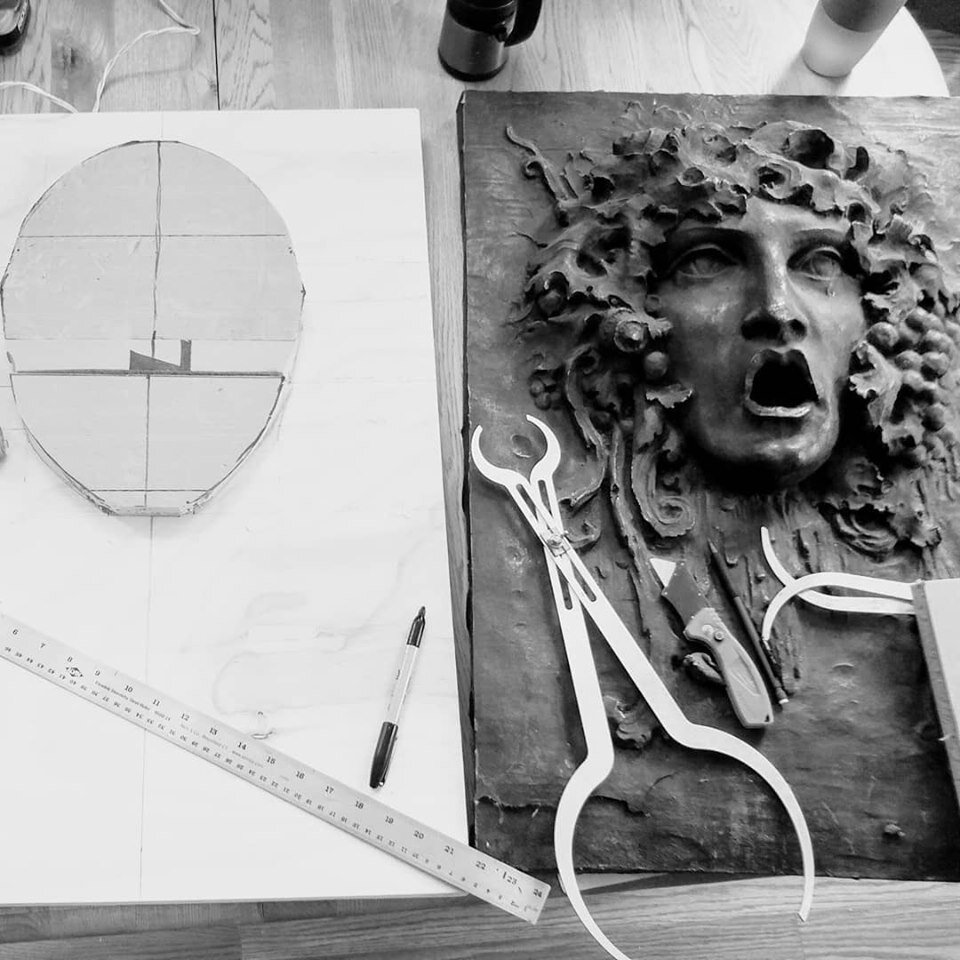
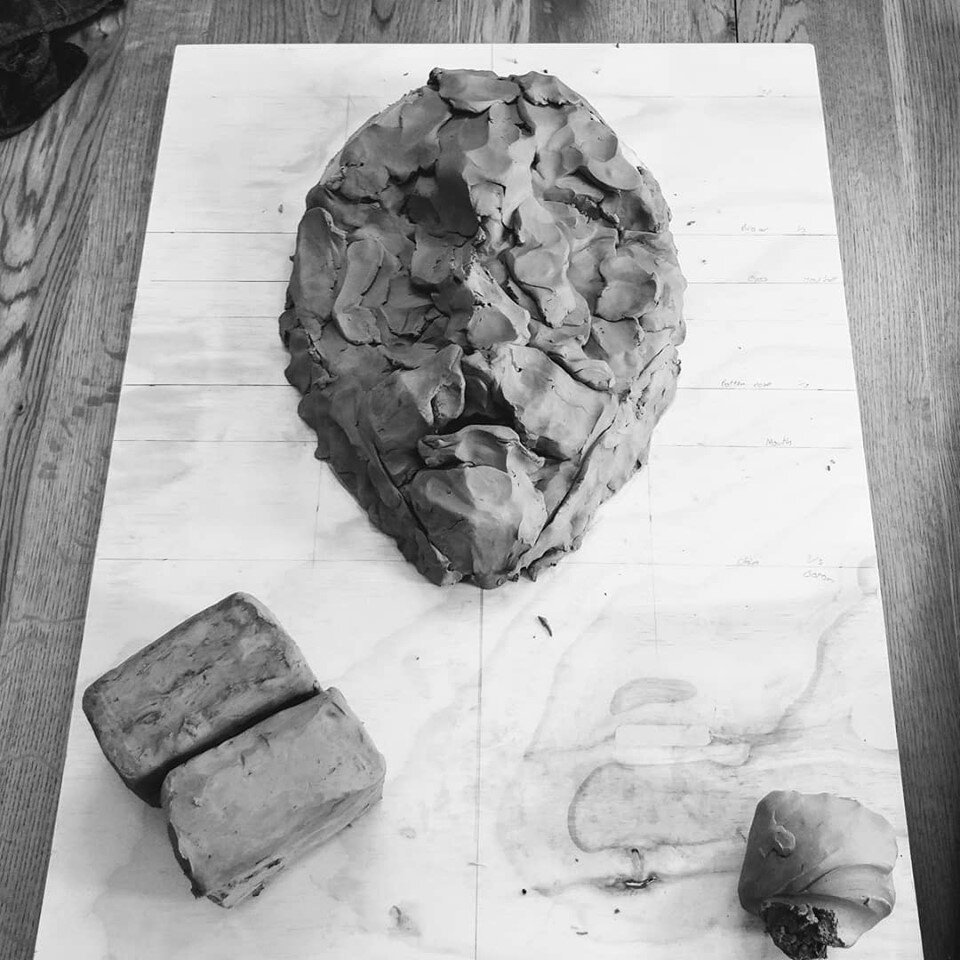
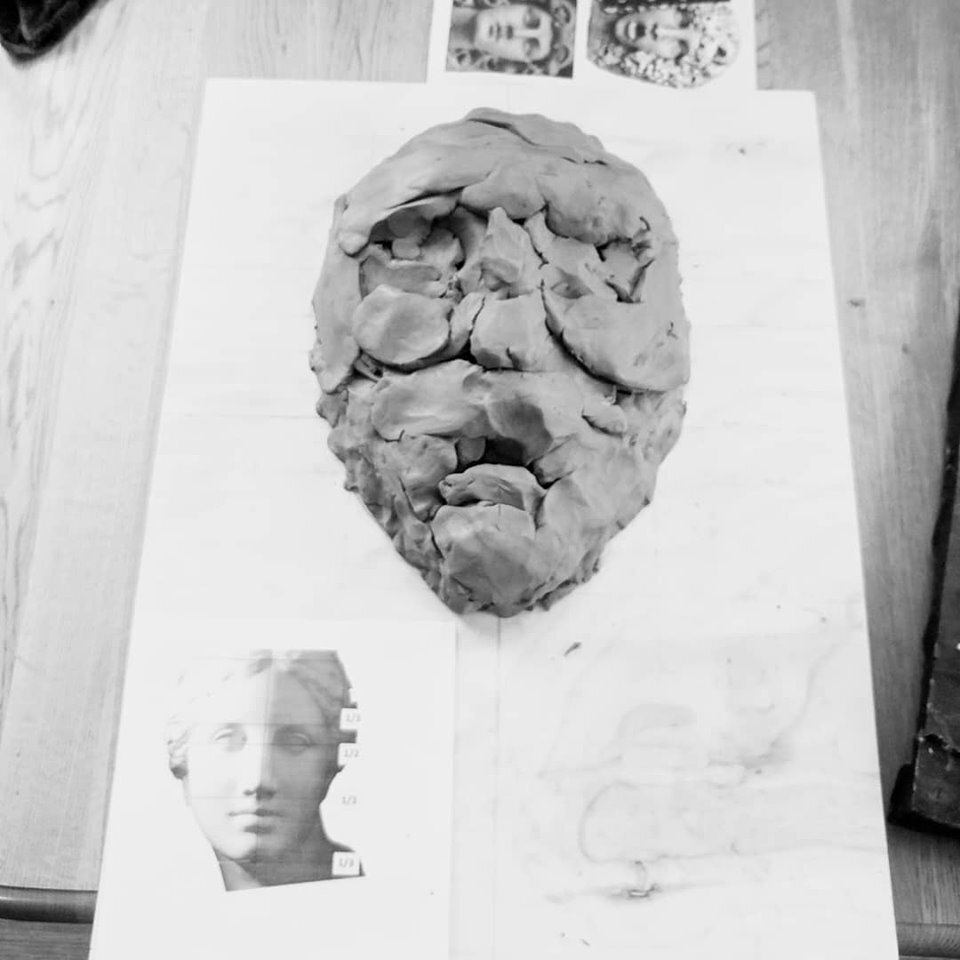
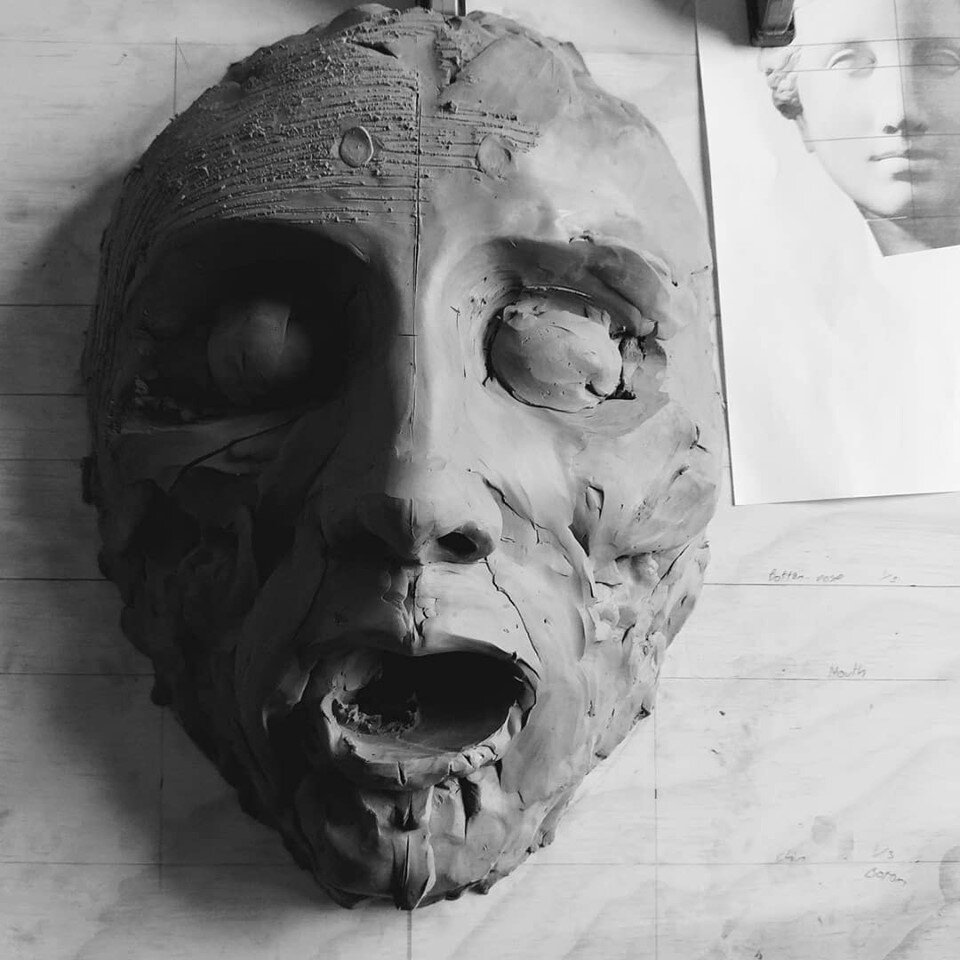
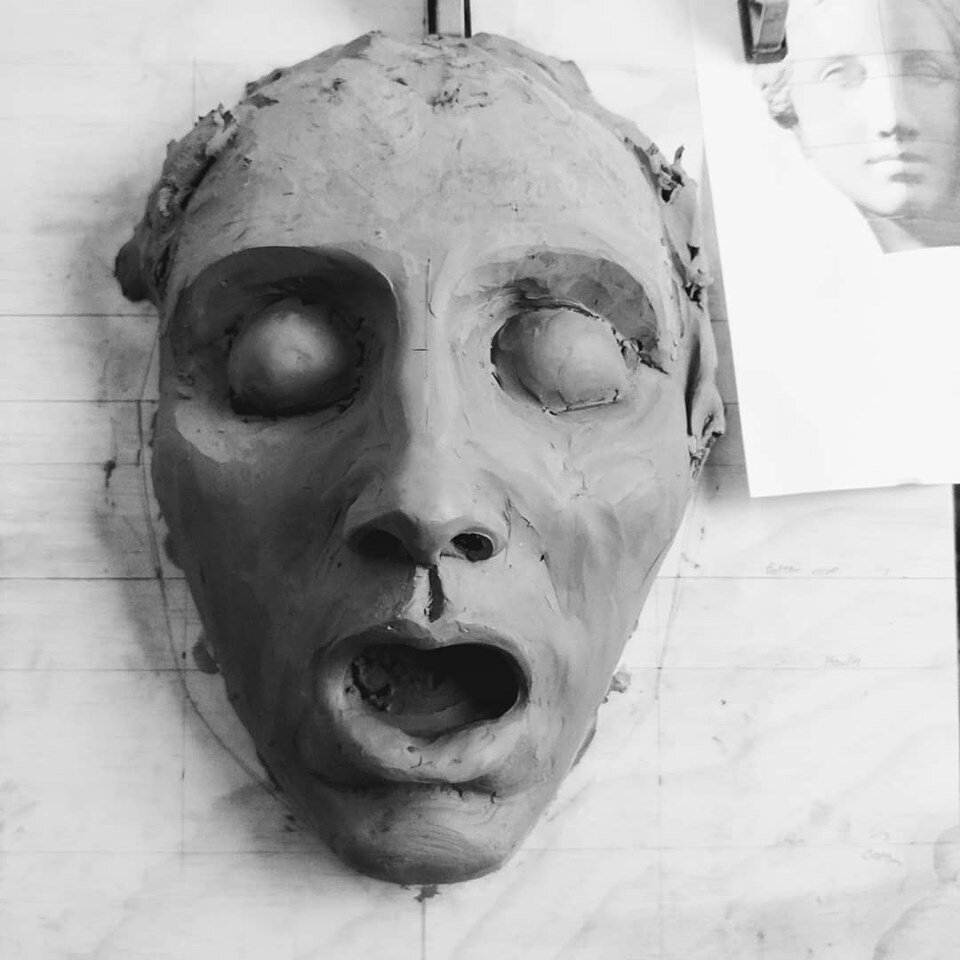
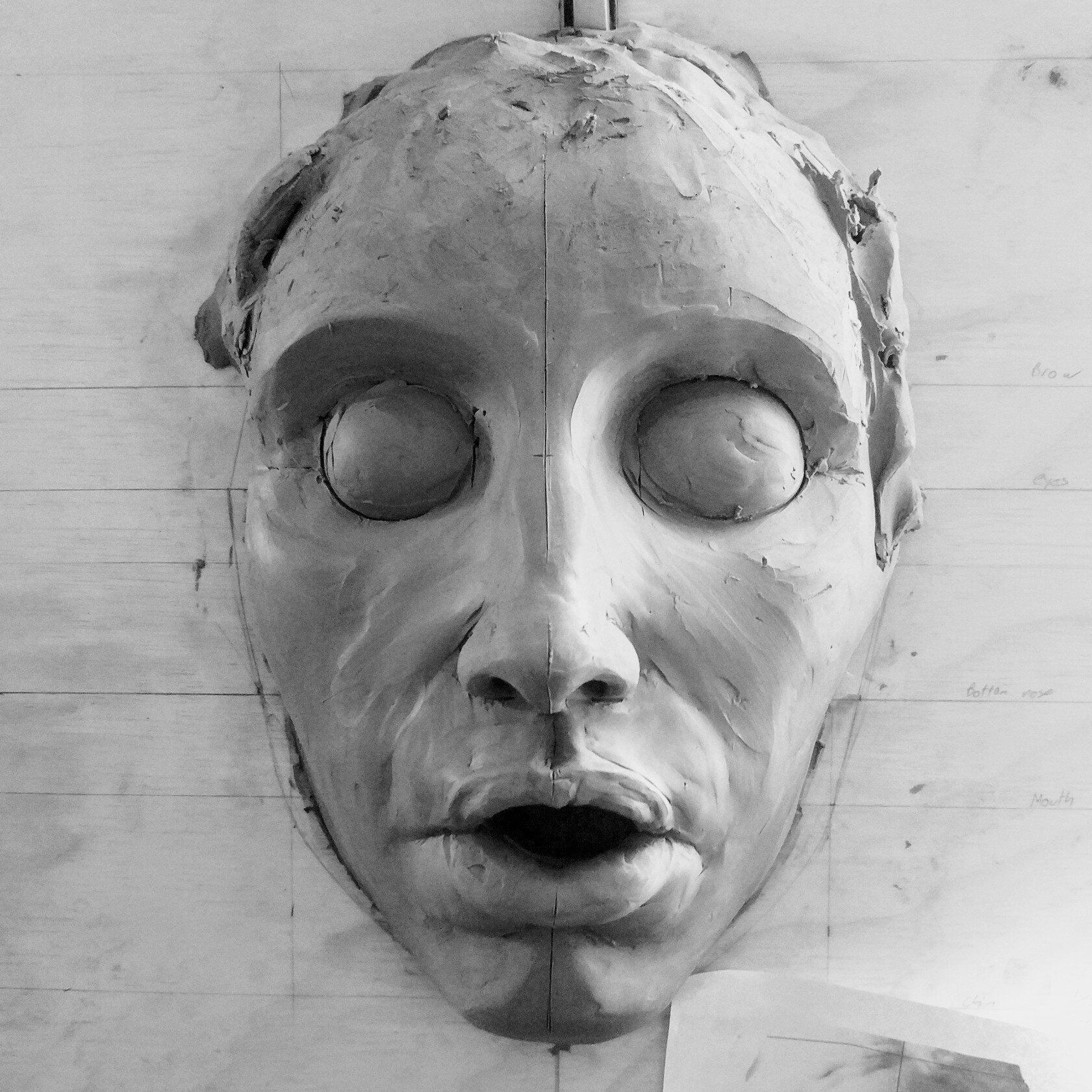
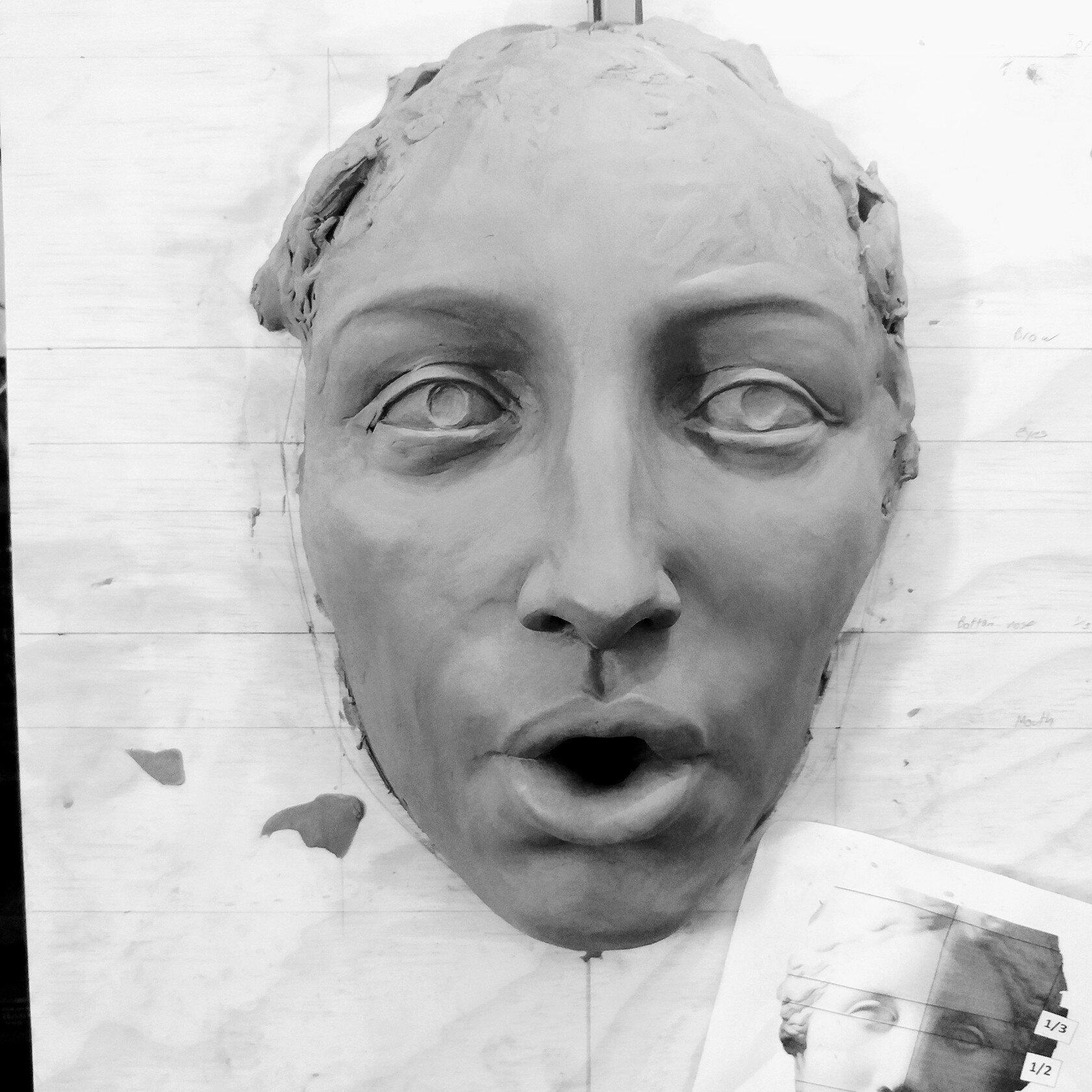
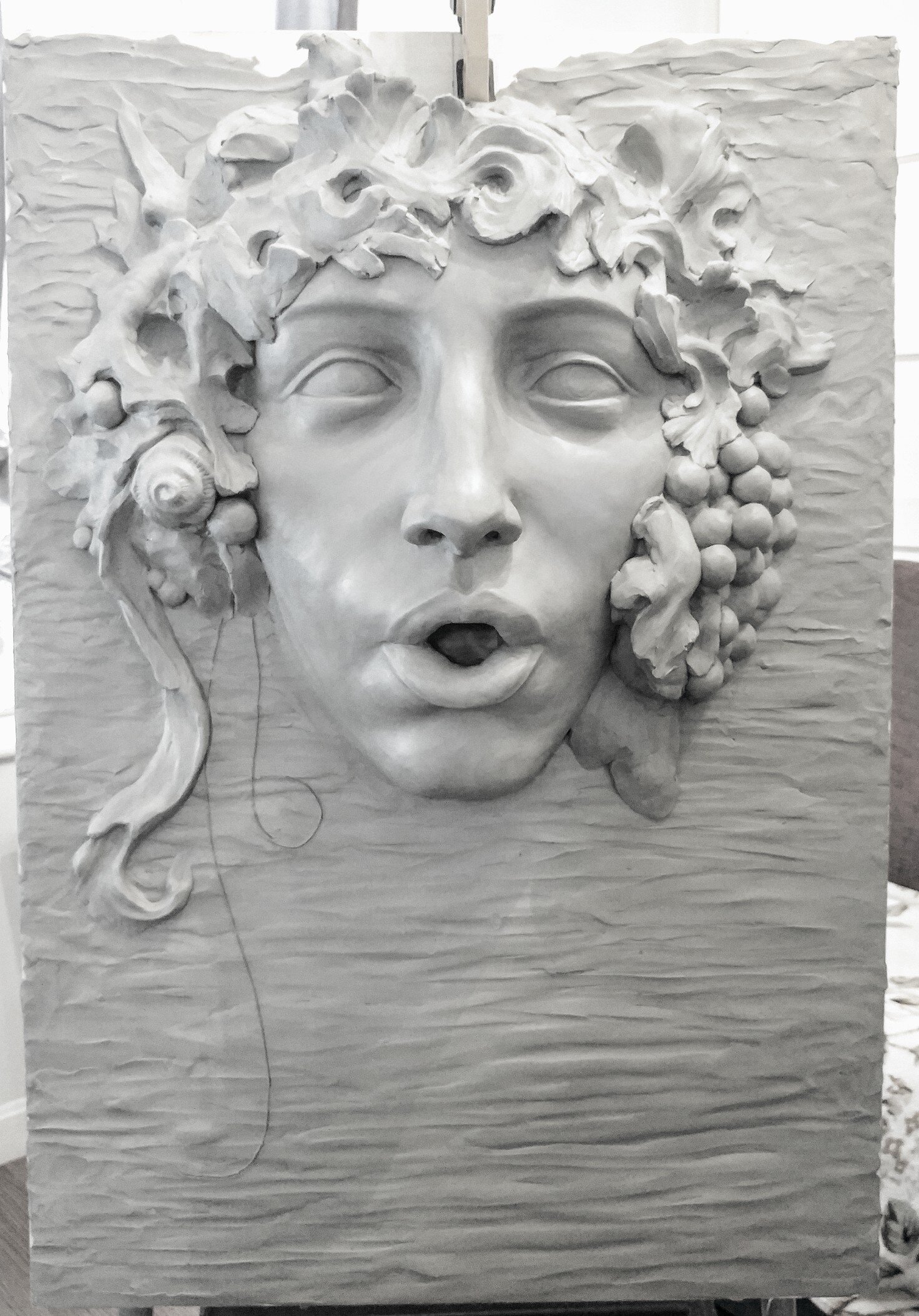
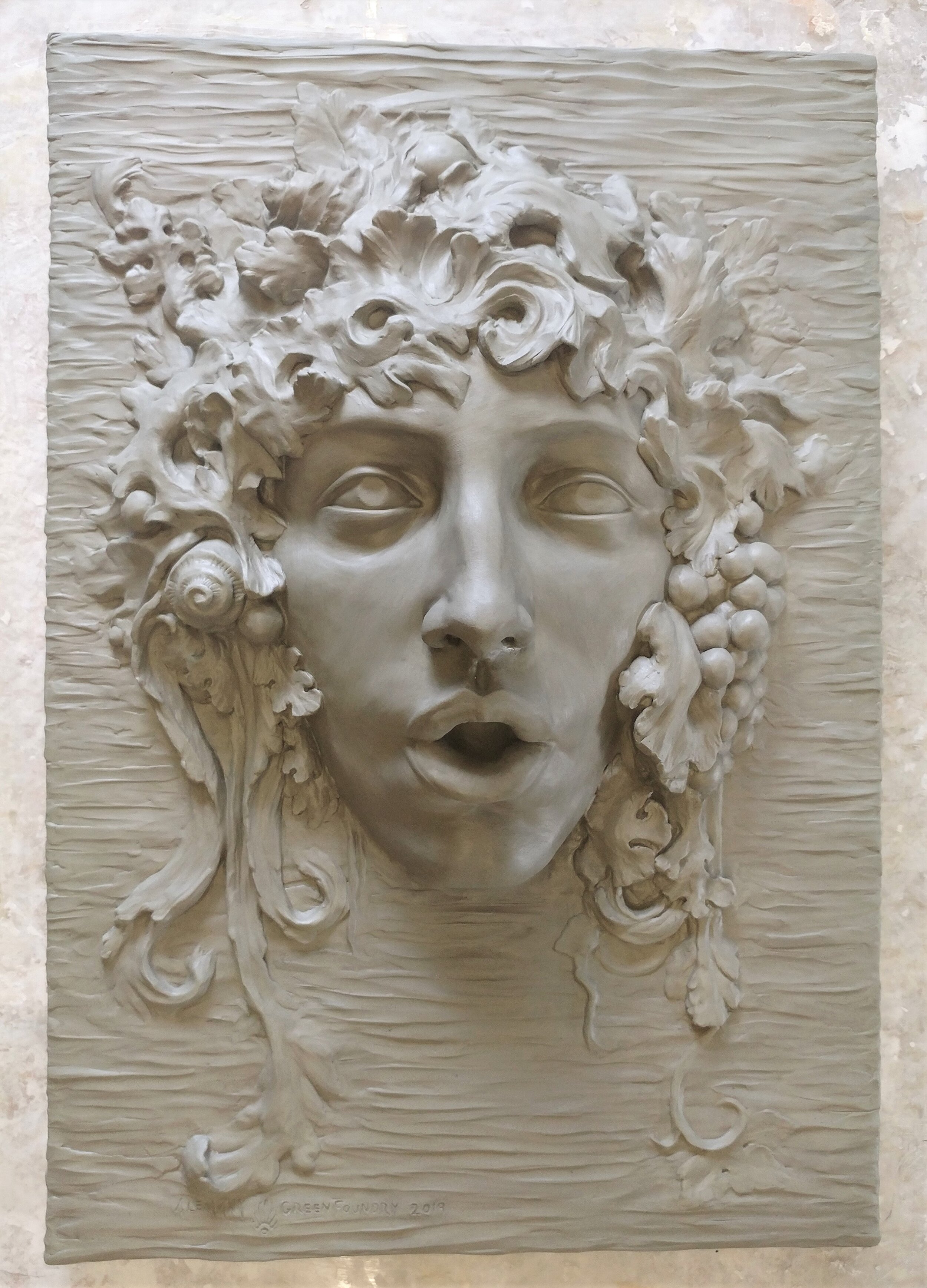
Mold-Making
After the clay-model meets approval, Anthony will create a mold. This will allow the sculpture to be reproduced in the desired medium. This process can take as little as a few days or as longs as a few weeks depending on the complexity of the project. (Click images to see process)
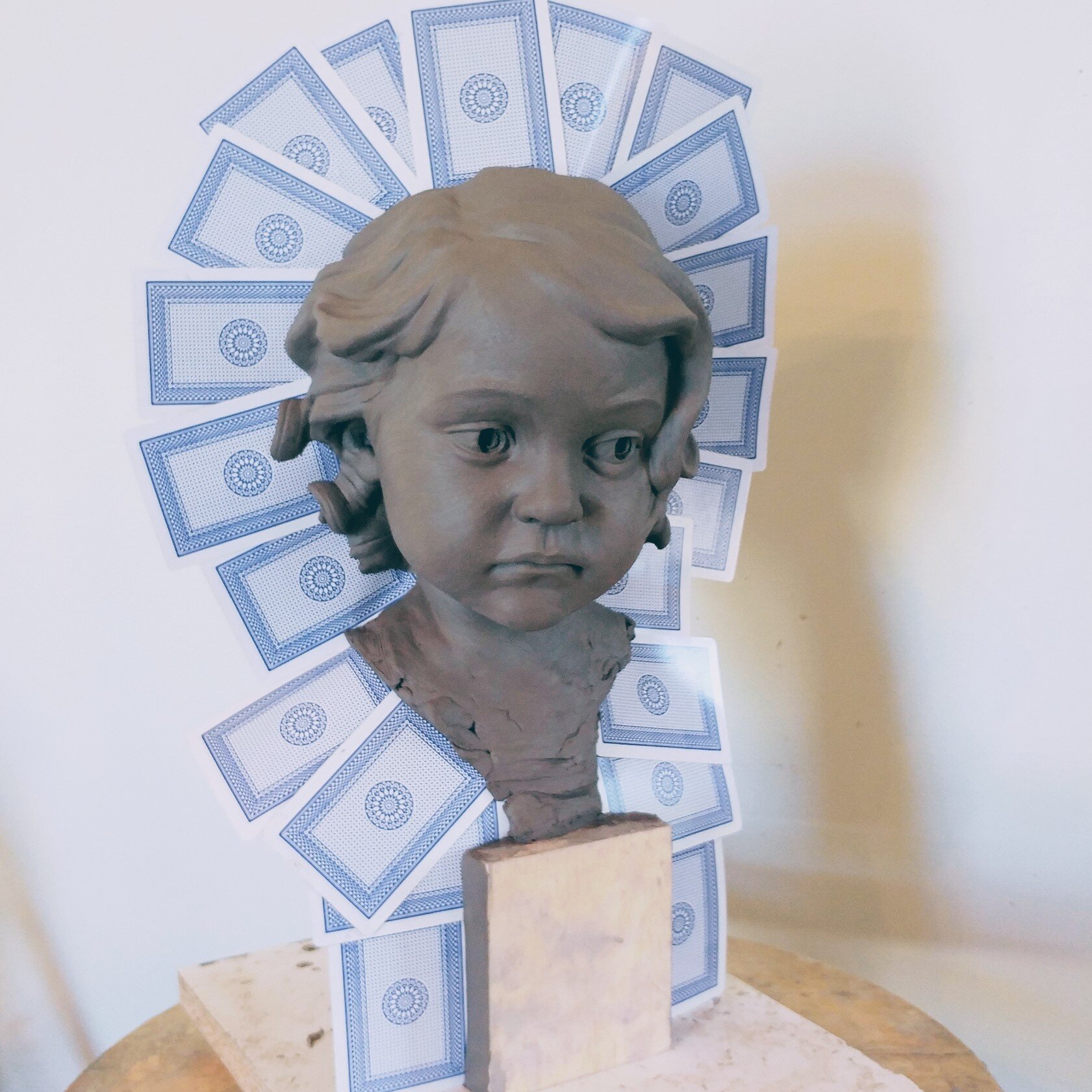
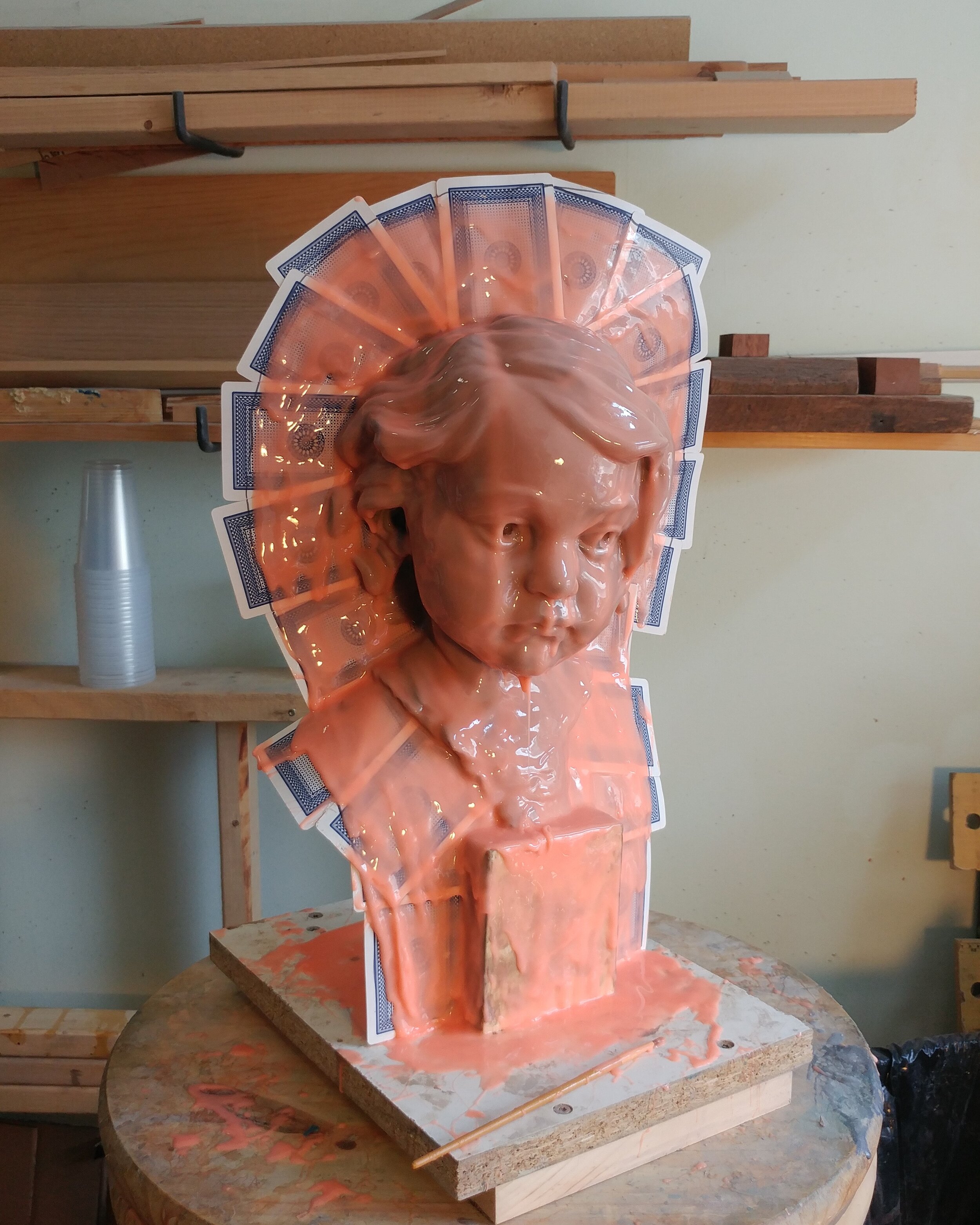
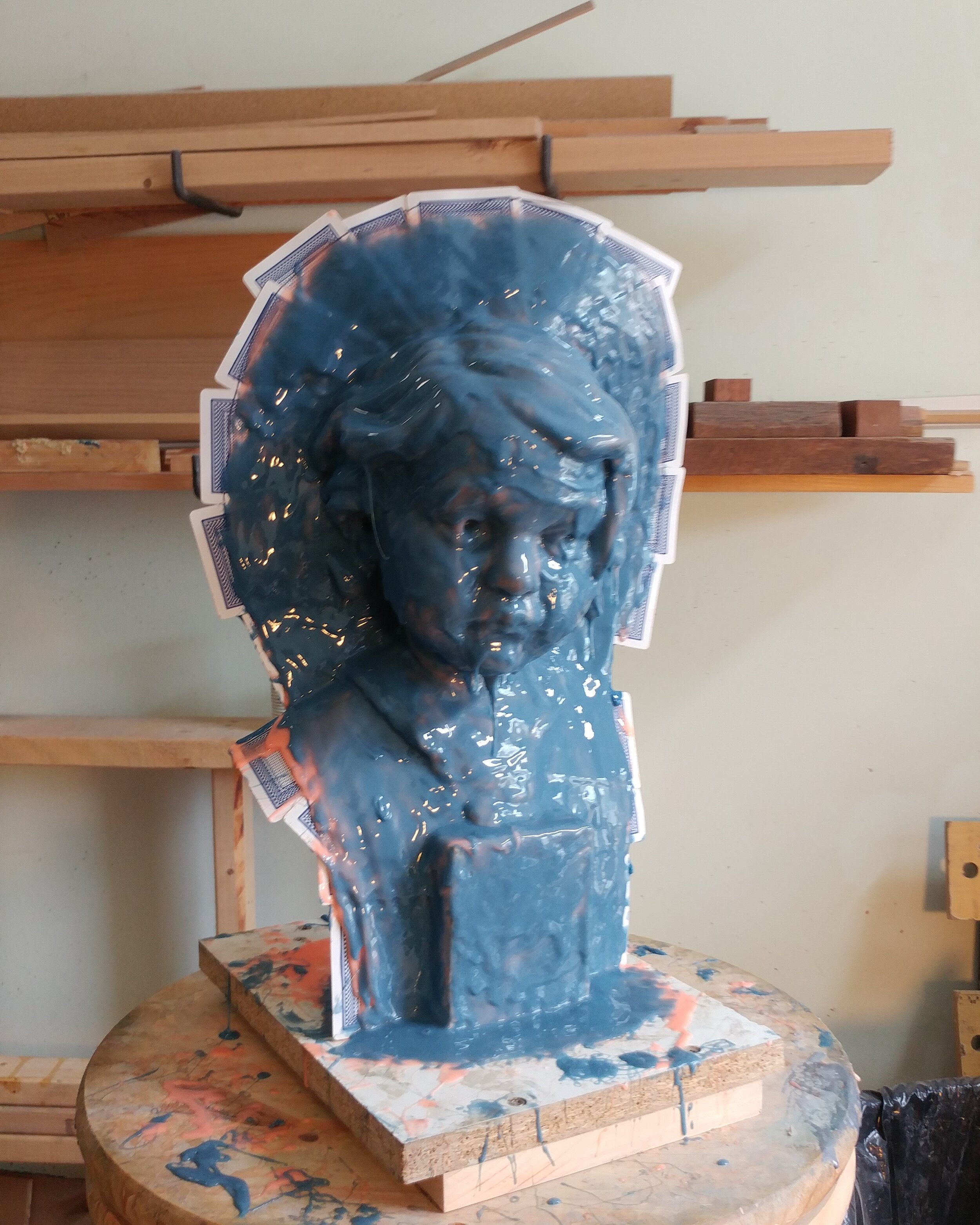
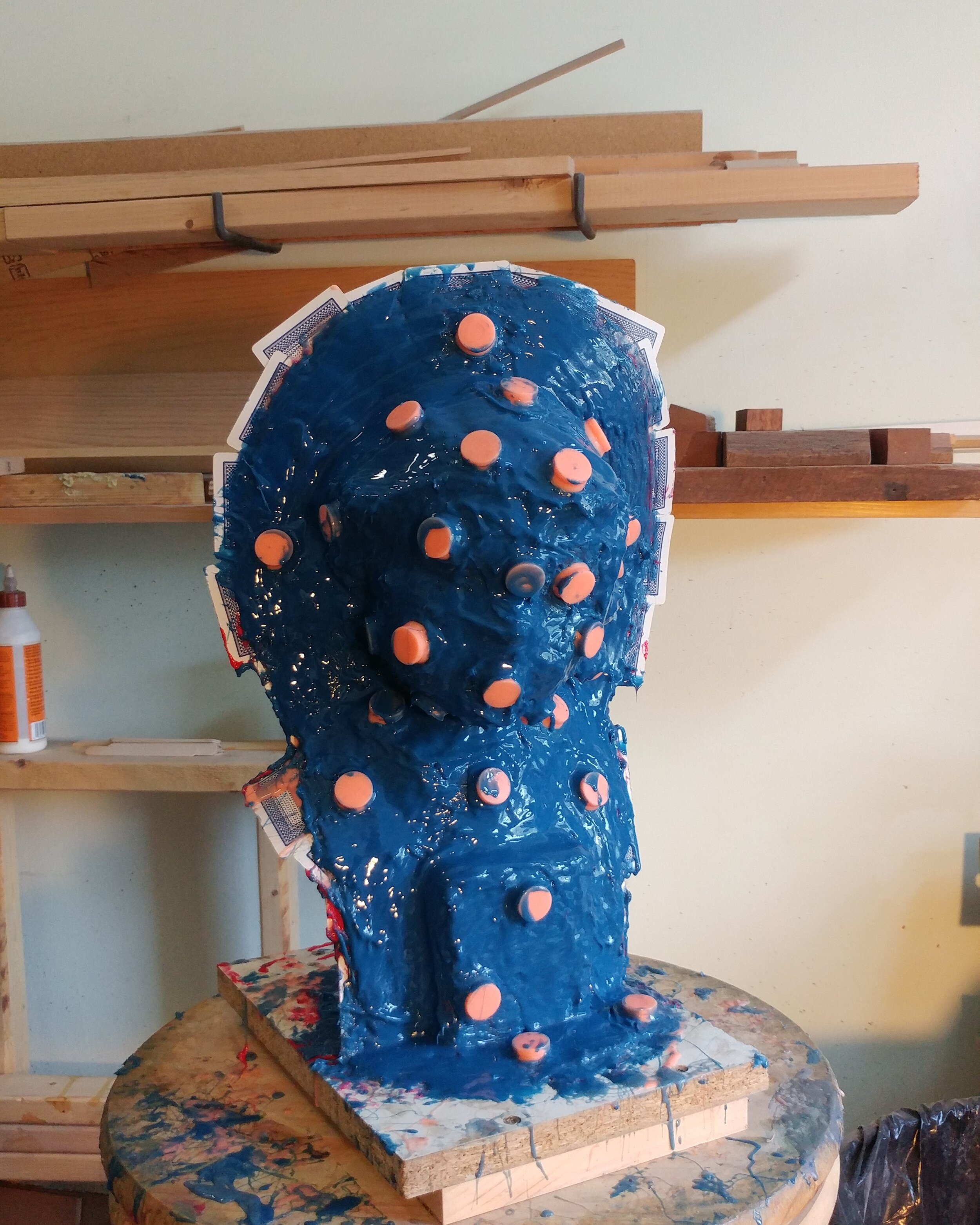
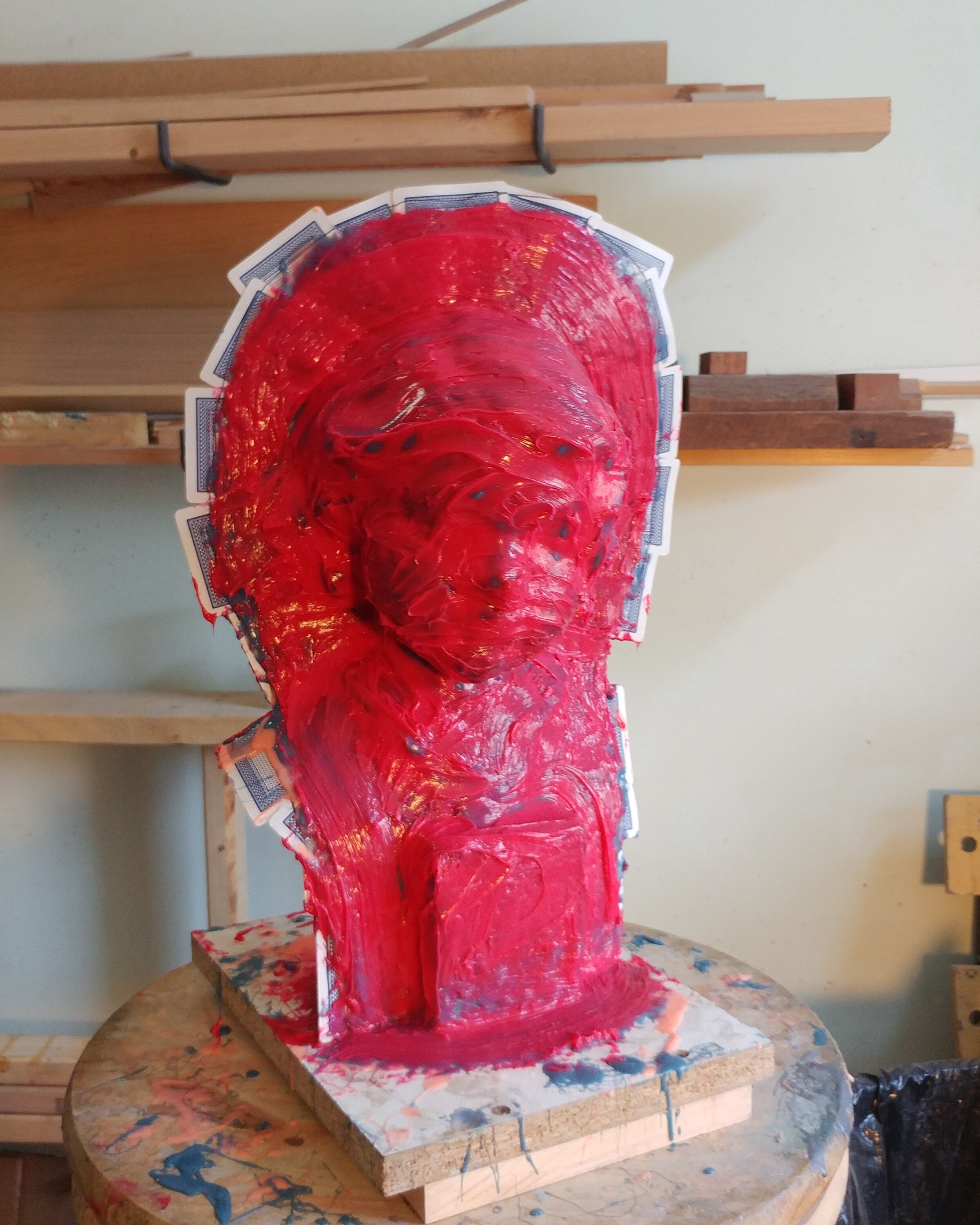
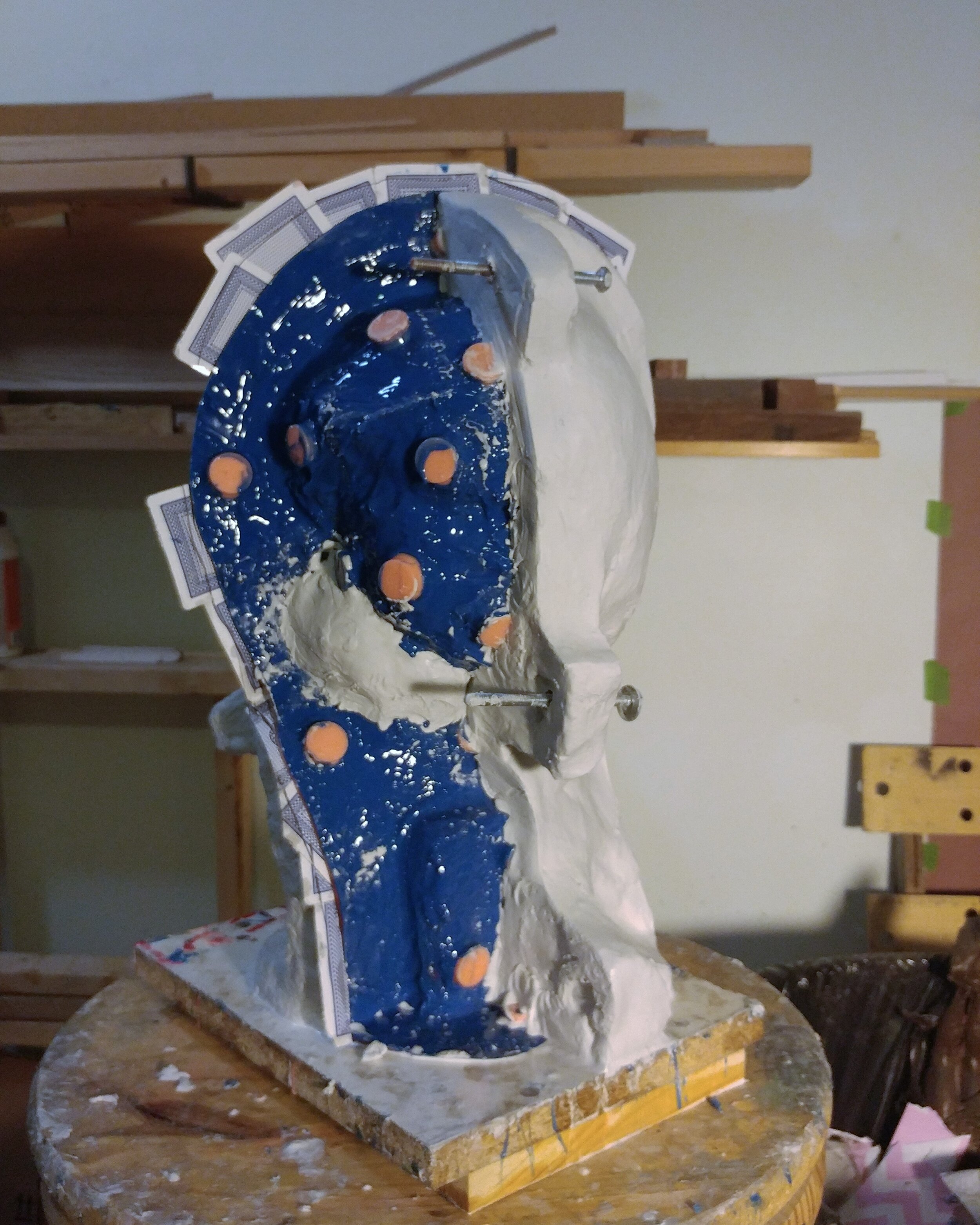
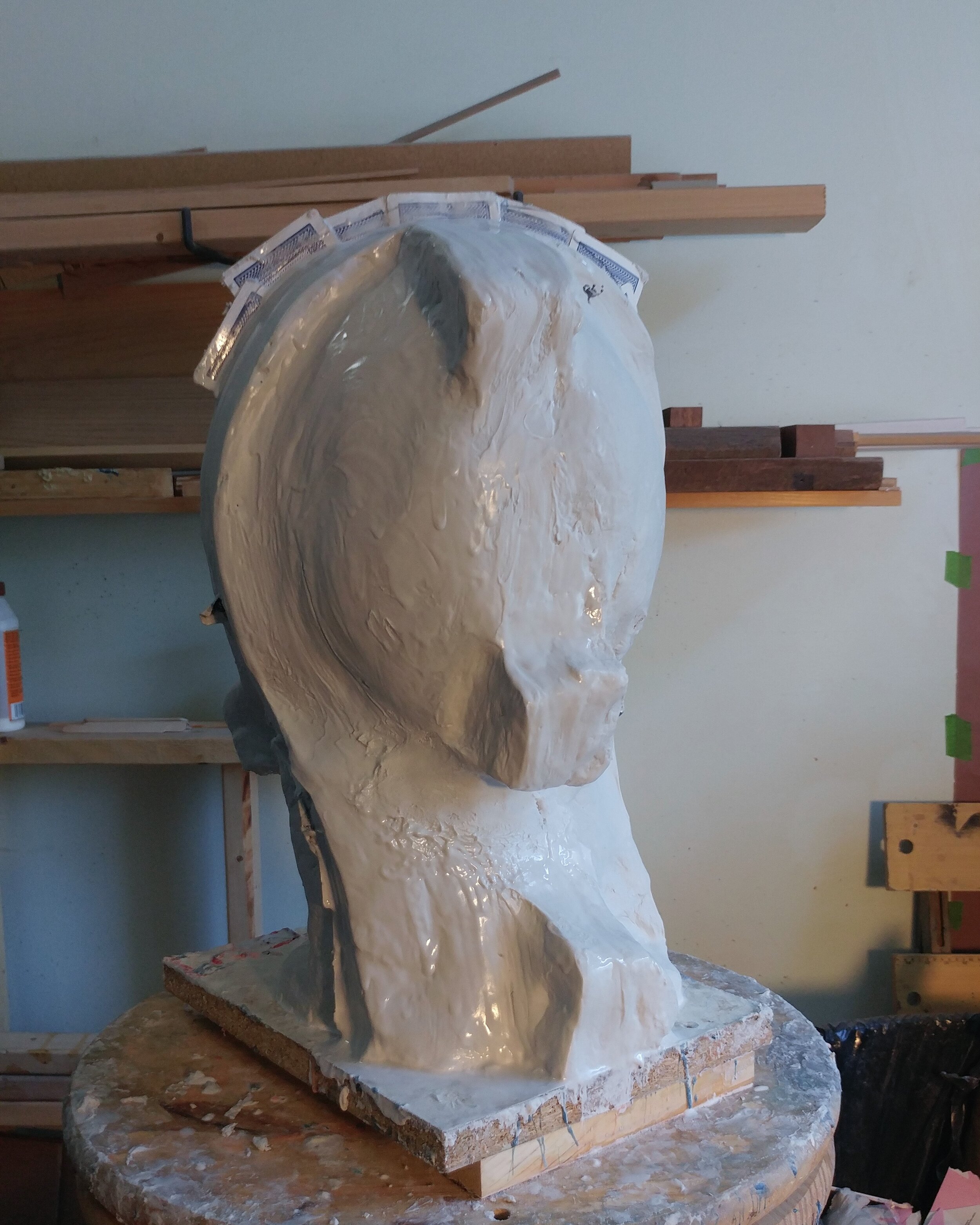

Wax Casting
A hollow wax casting is made from the mold. This is the final positive before the bronze. Every form and detail, down to the thickness of the wax will directly translate into the bronze. The wax casting is refined to remove any defects from the casting process. Then the wax is cut into pieces to facilitate the bronze pour. Sprues and gates are attached to the pieces and a wax cup is attached to the top to create what is called a tree. The sprues and gates create channels to control the flow of liquid metal during the pour. This process can take a few days or a few weeks depending on the complexity of the sculpture. (Click images to see process)
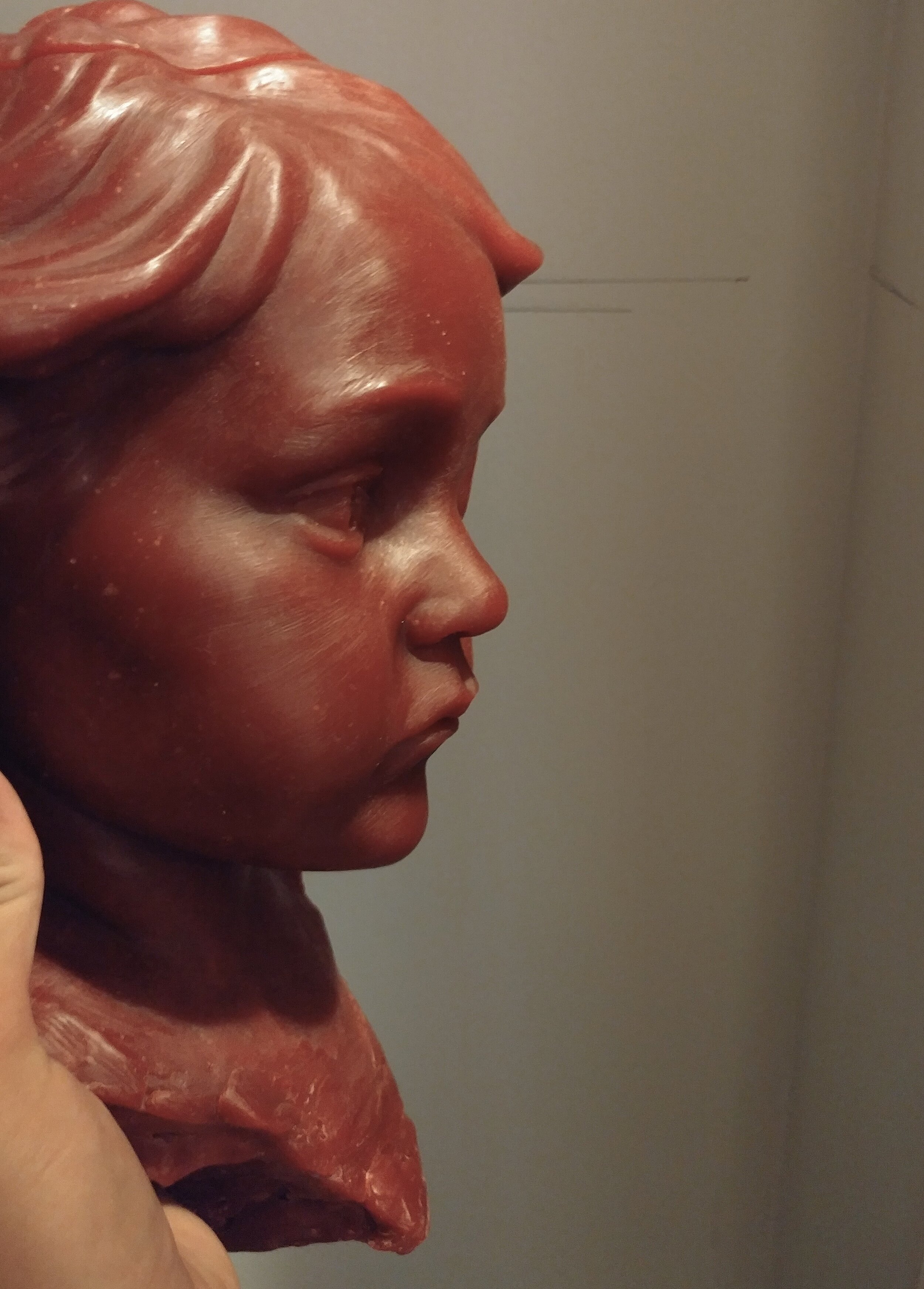
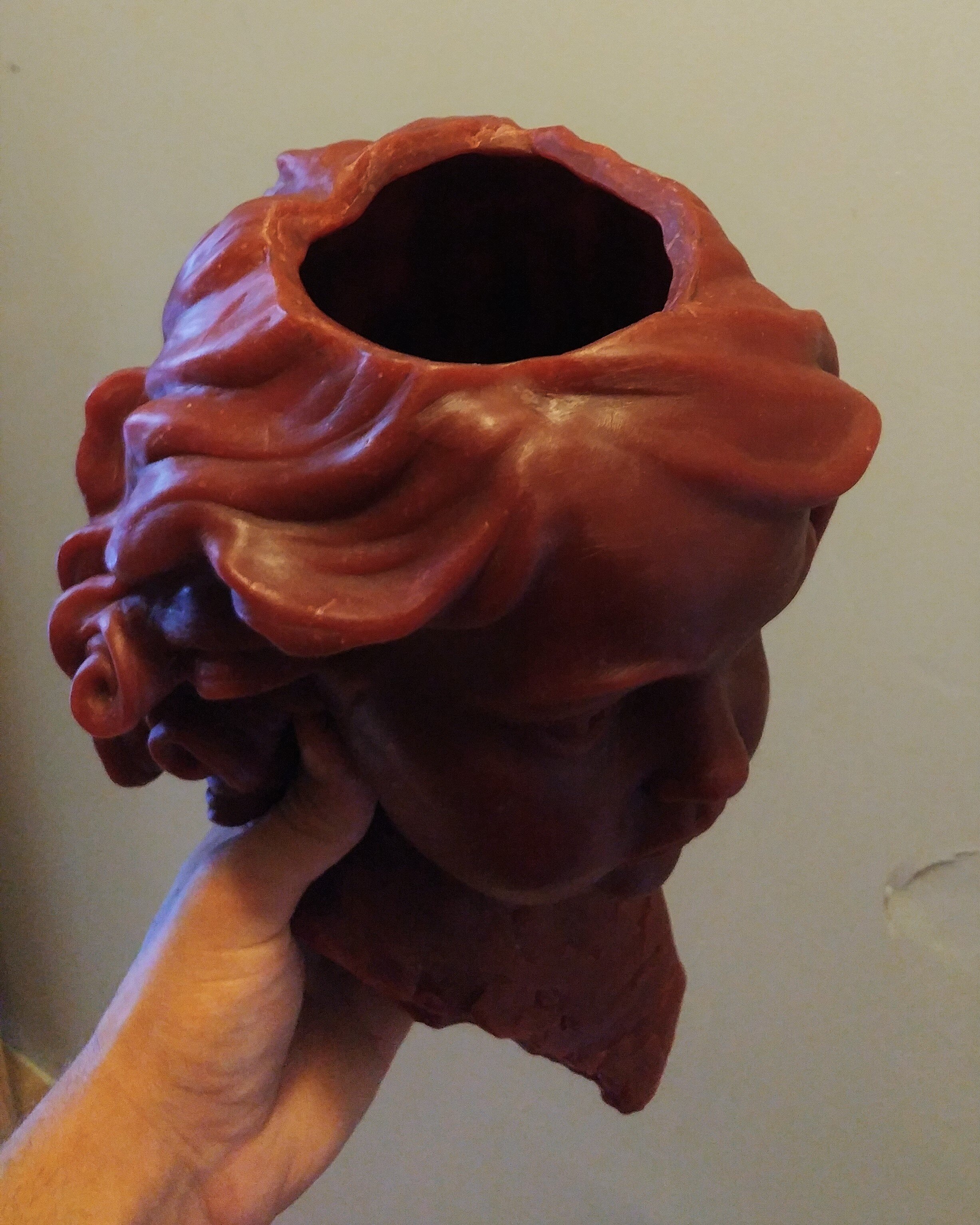
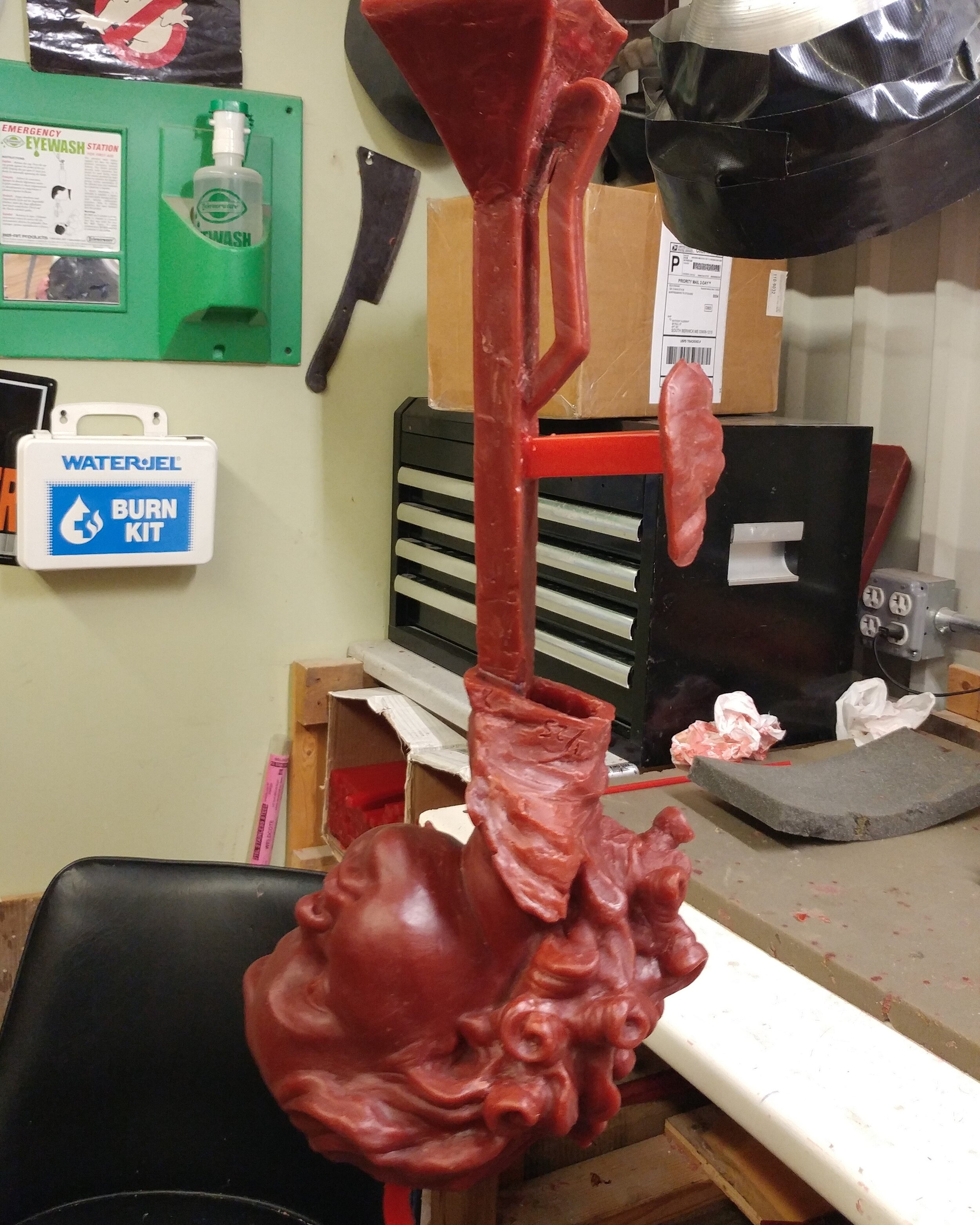
Ceramic-Shell
Once the wax process is complete, a ceramic mold is made around it. This is the final negative before the pour. The mold is slowly created over 2-3 weeks with 12-16 coats of silica-slurry, usually one coat per day. The wax is dipped into the liquid slurry, removed, and silica sand is applied to build the thickness mold. Once the layers are complete and the desired thickness is achieved, the silica molds are left to dry and are then fired. This melts out the wax creating the negative space for the metal to flow and transforms the silica into a ceramic-shell capable of withstanding the temperature of molten metal. (Click images to see process)
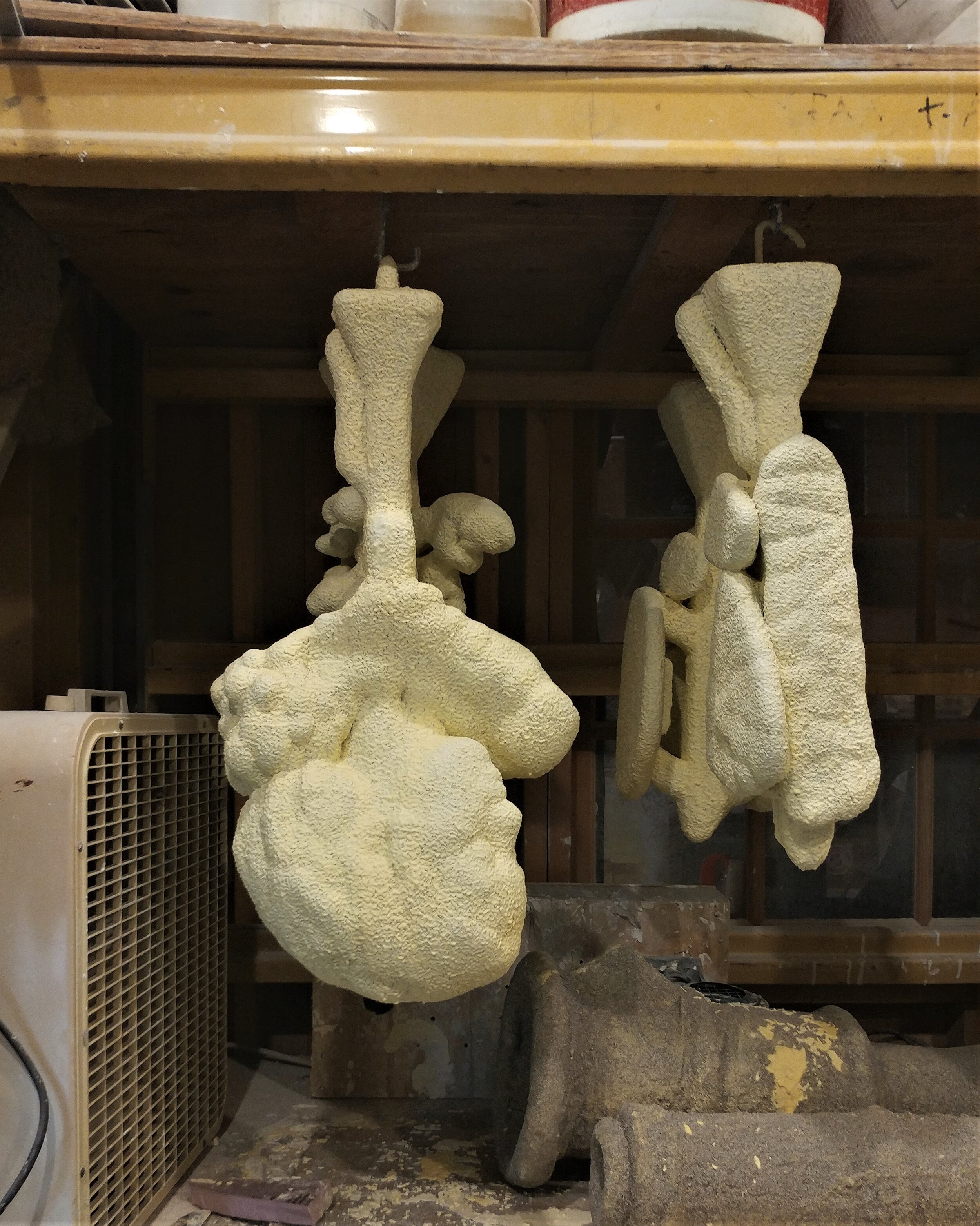
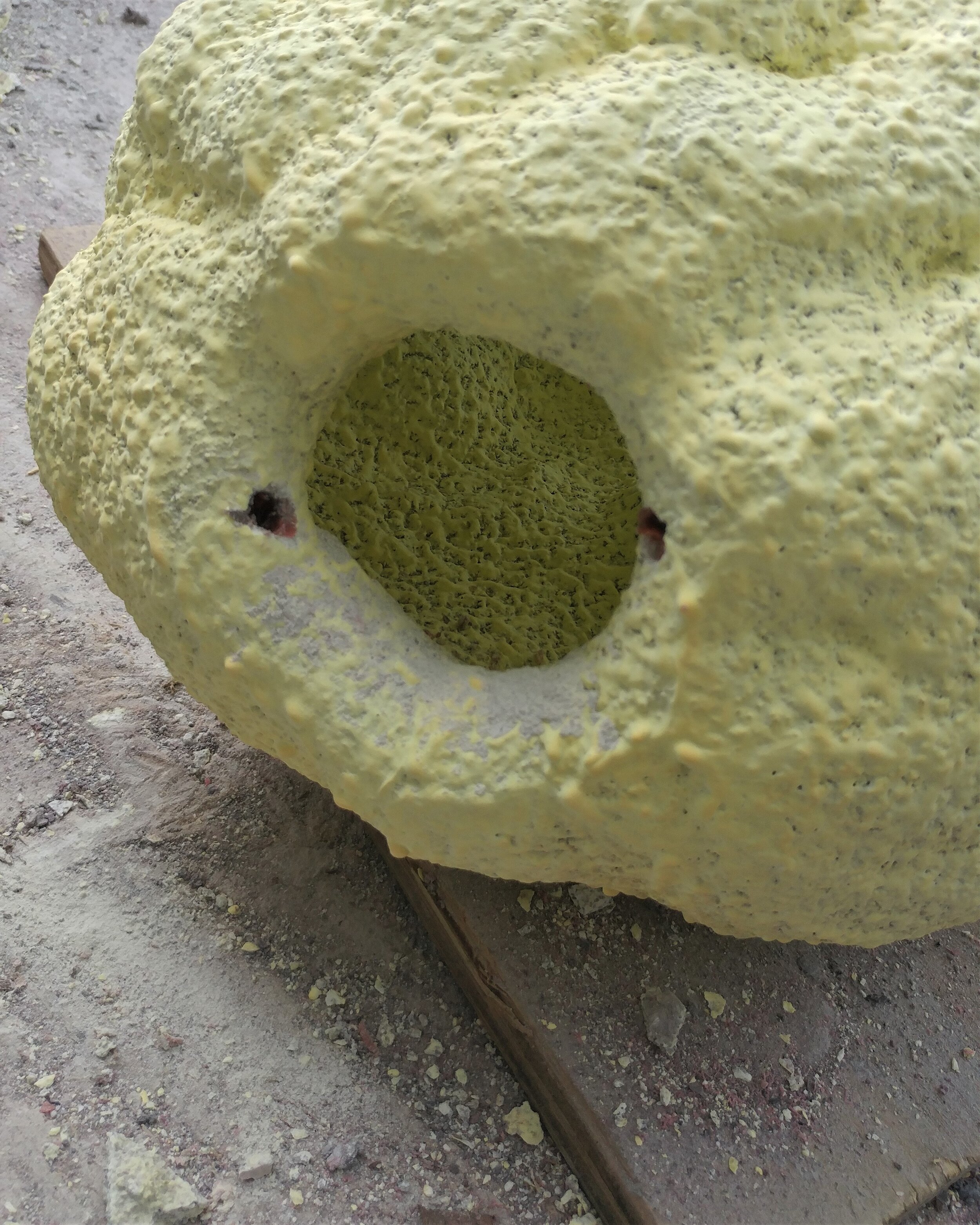
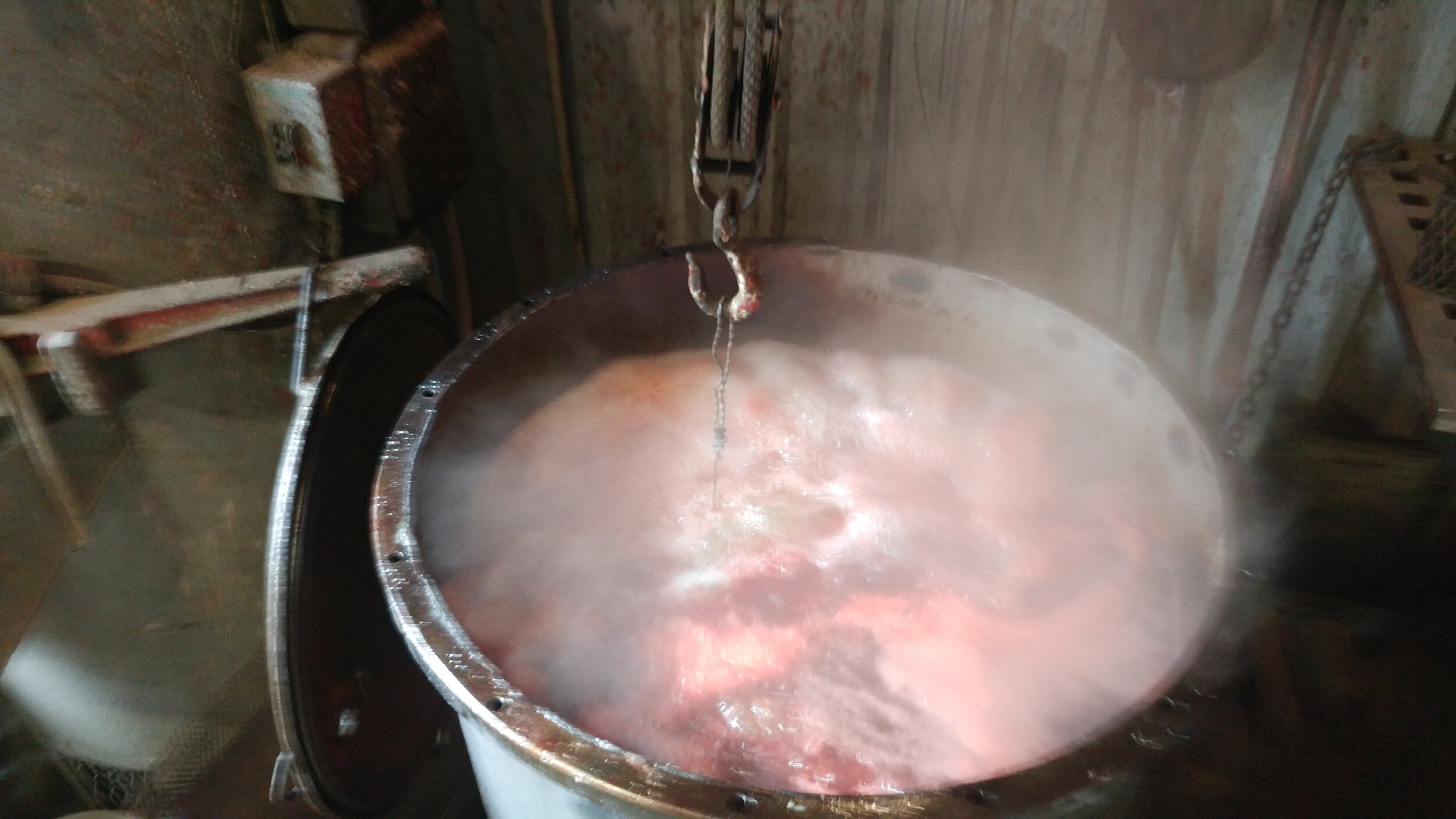
Bronze pour
The melting point for silicon-bronze is around 1800oF / 980oC. The ceramic shell is heated to around 1000oF / 550oC and then the molten bronze is poured into the mold. (Click images to see process)
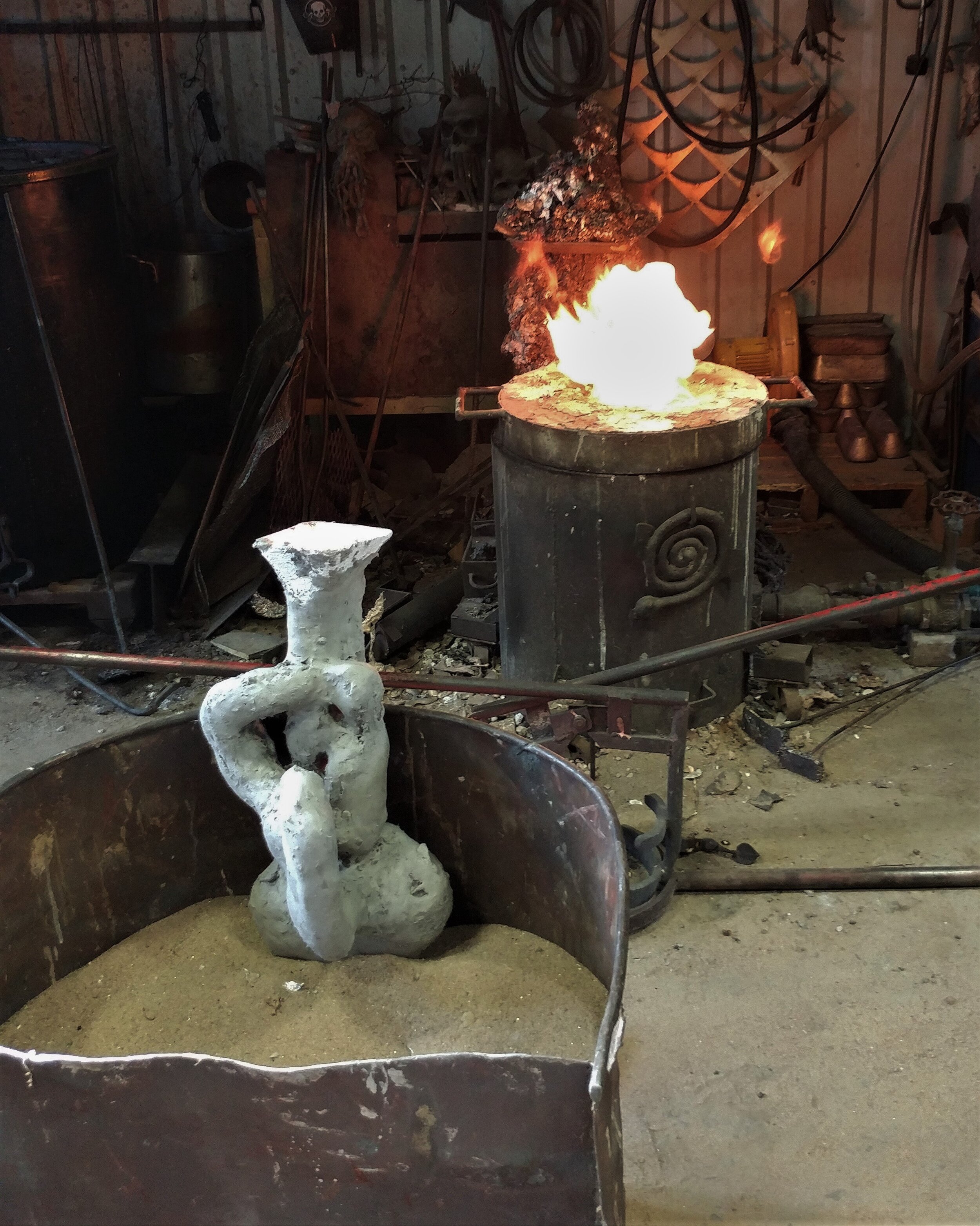
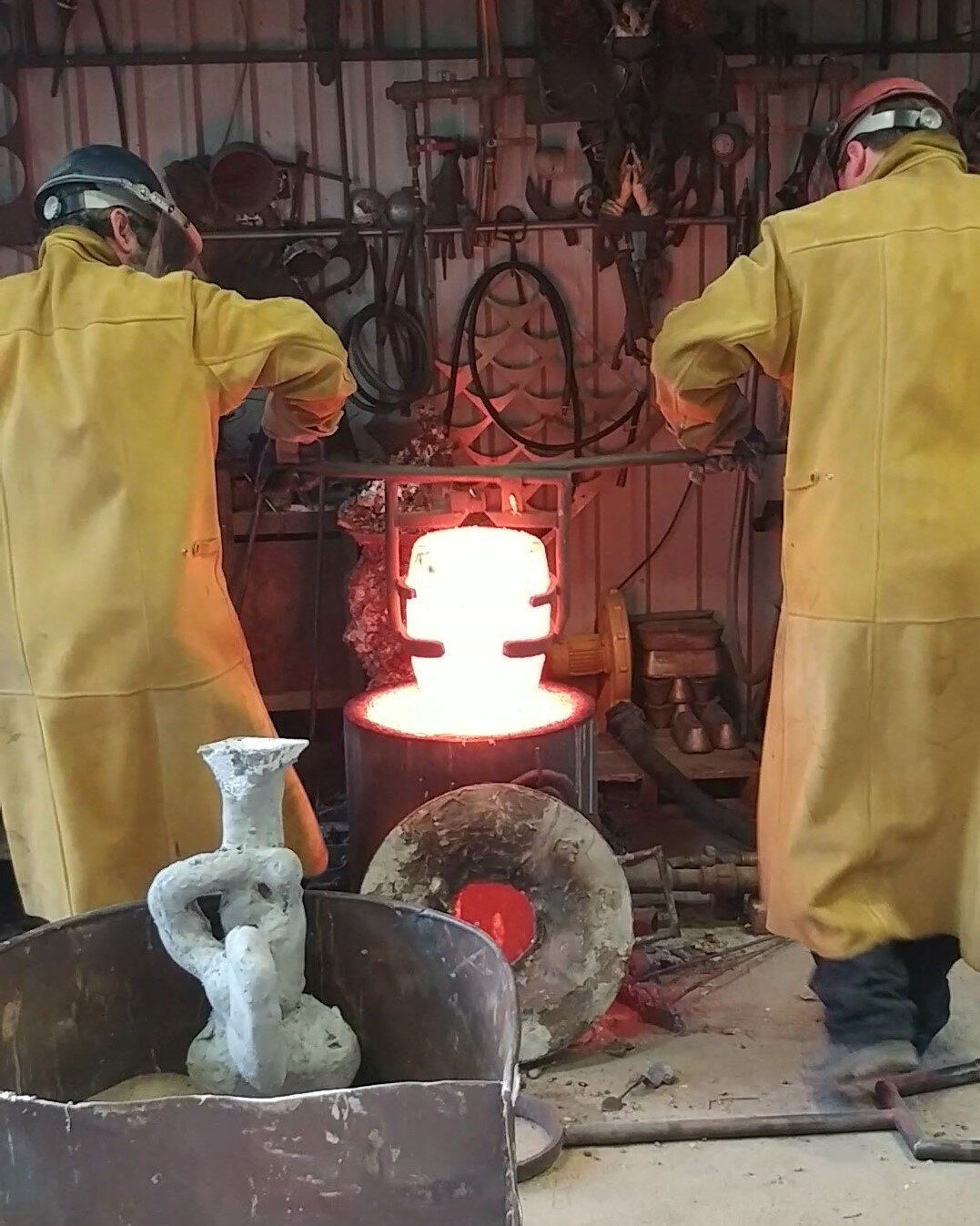
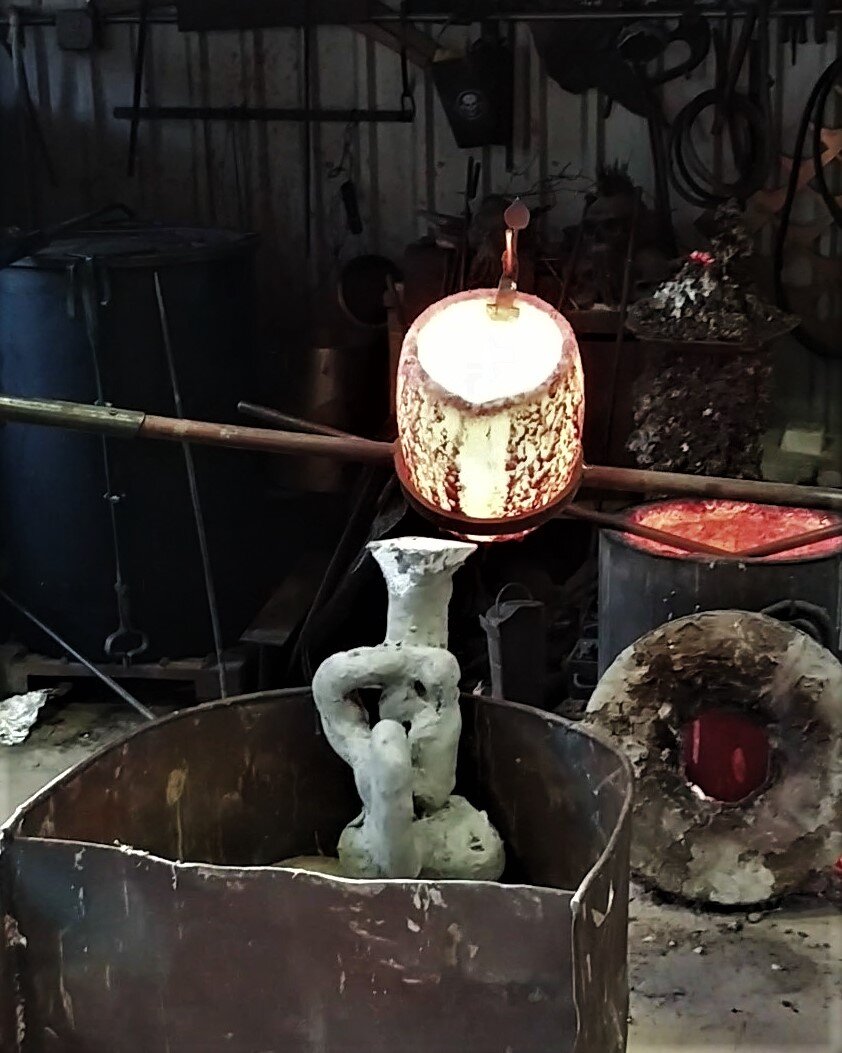
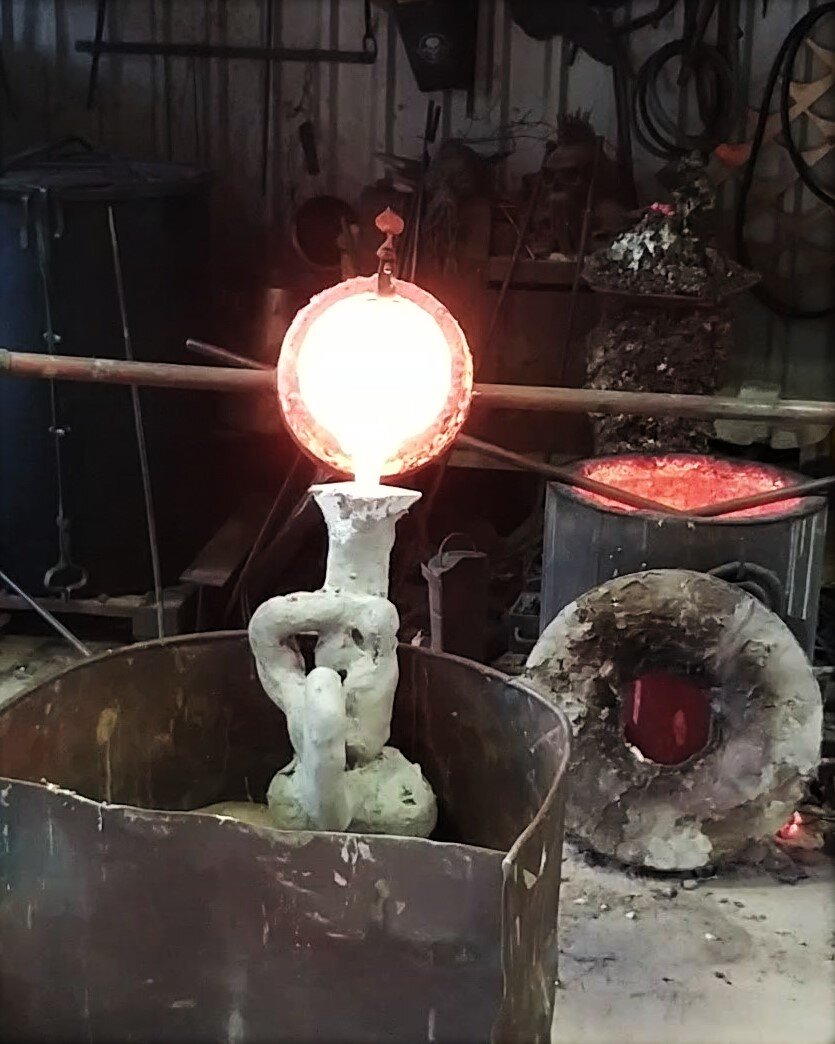
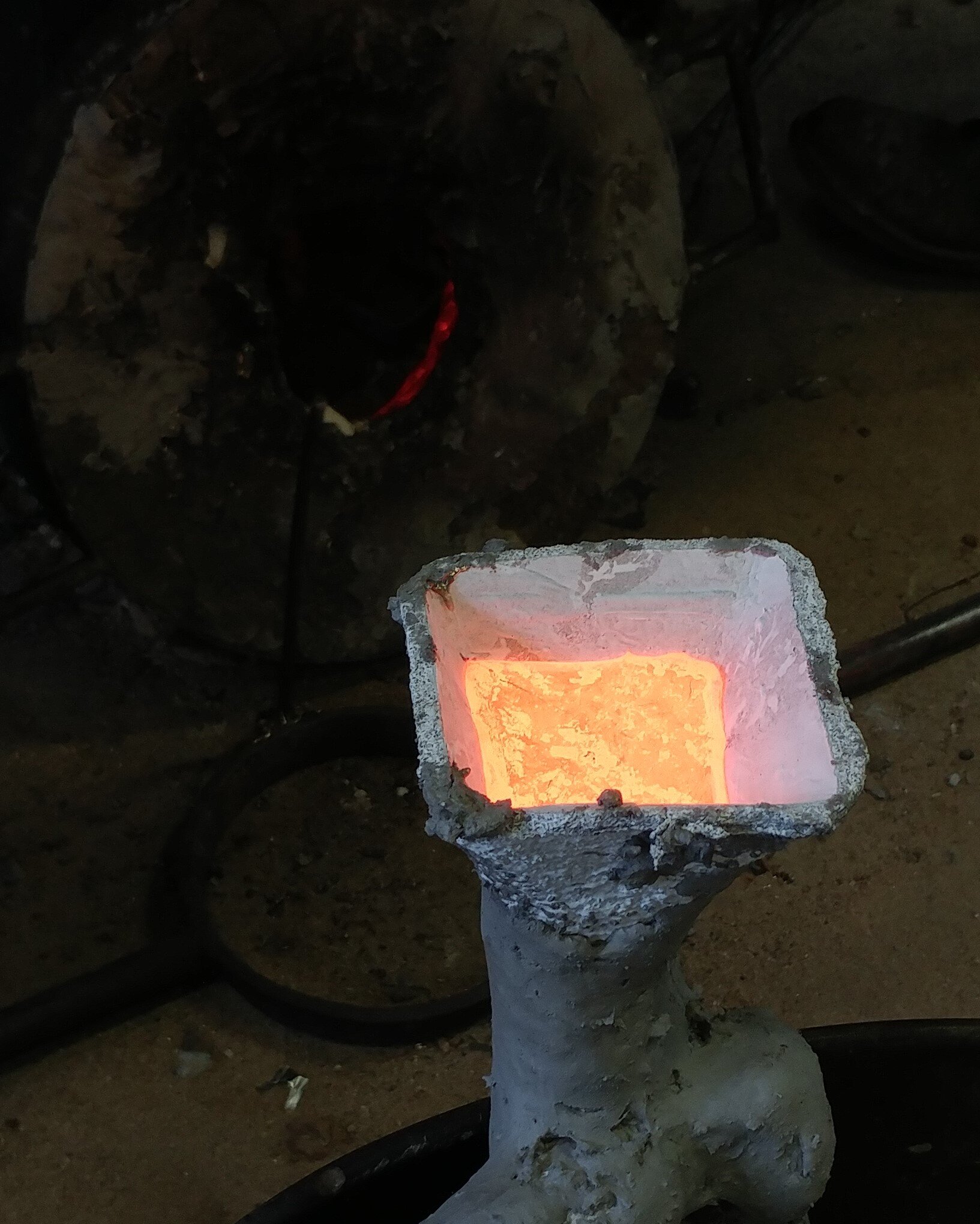
Chasing
After the casting has cooled, the ceramic shell is broken away and the metal sprues and gates are cut off. Then the pieces are welded together. Any welds and casting imperfections are ground away, tooled and re-textured to match the original sculpture. This is an arduous process and can take several weeks. The sculpture is drilled and tapped to install the necessary hardware for installation. (Click images to see process)
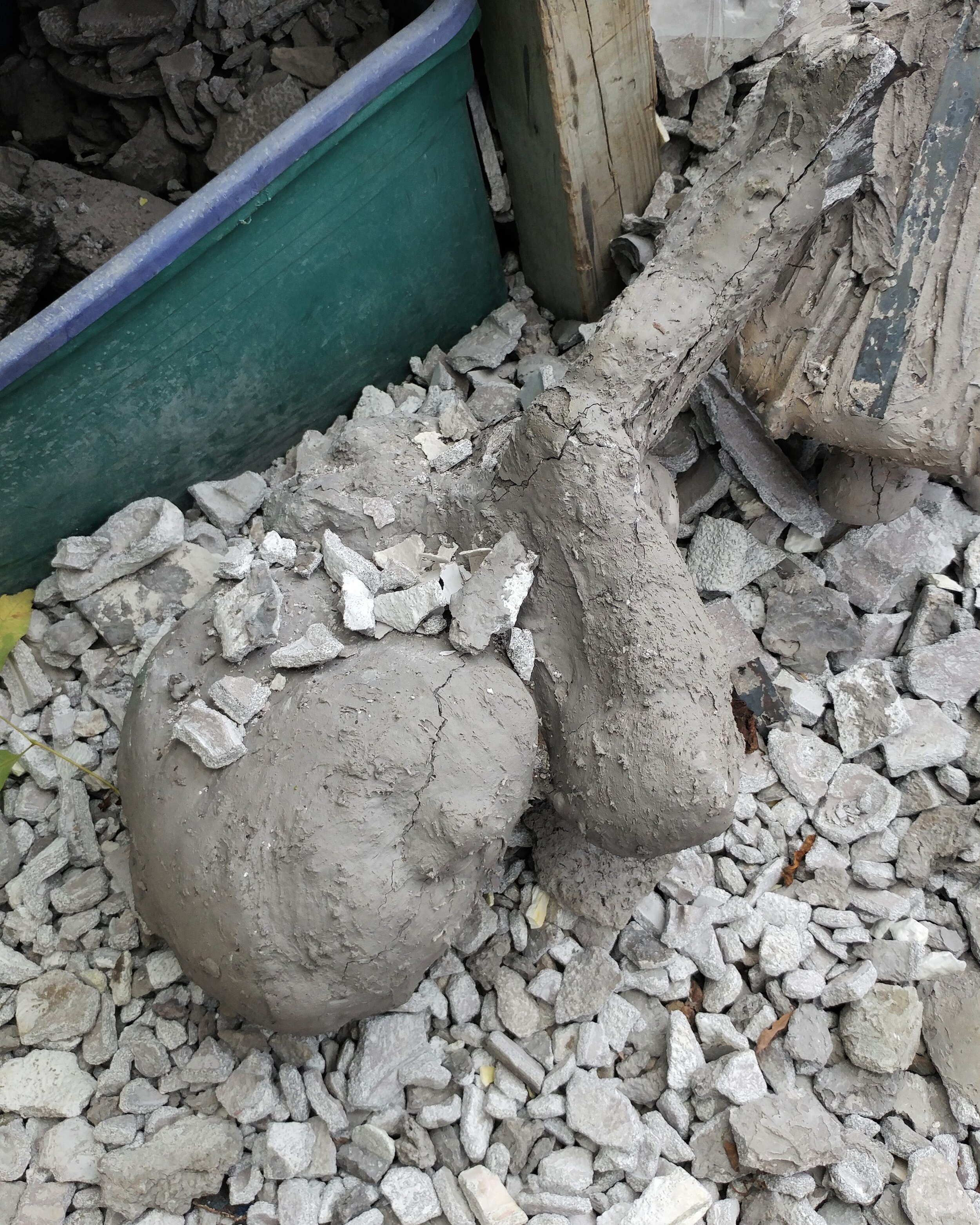
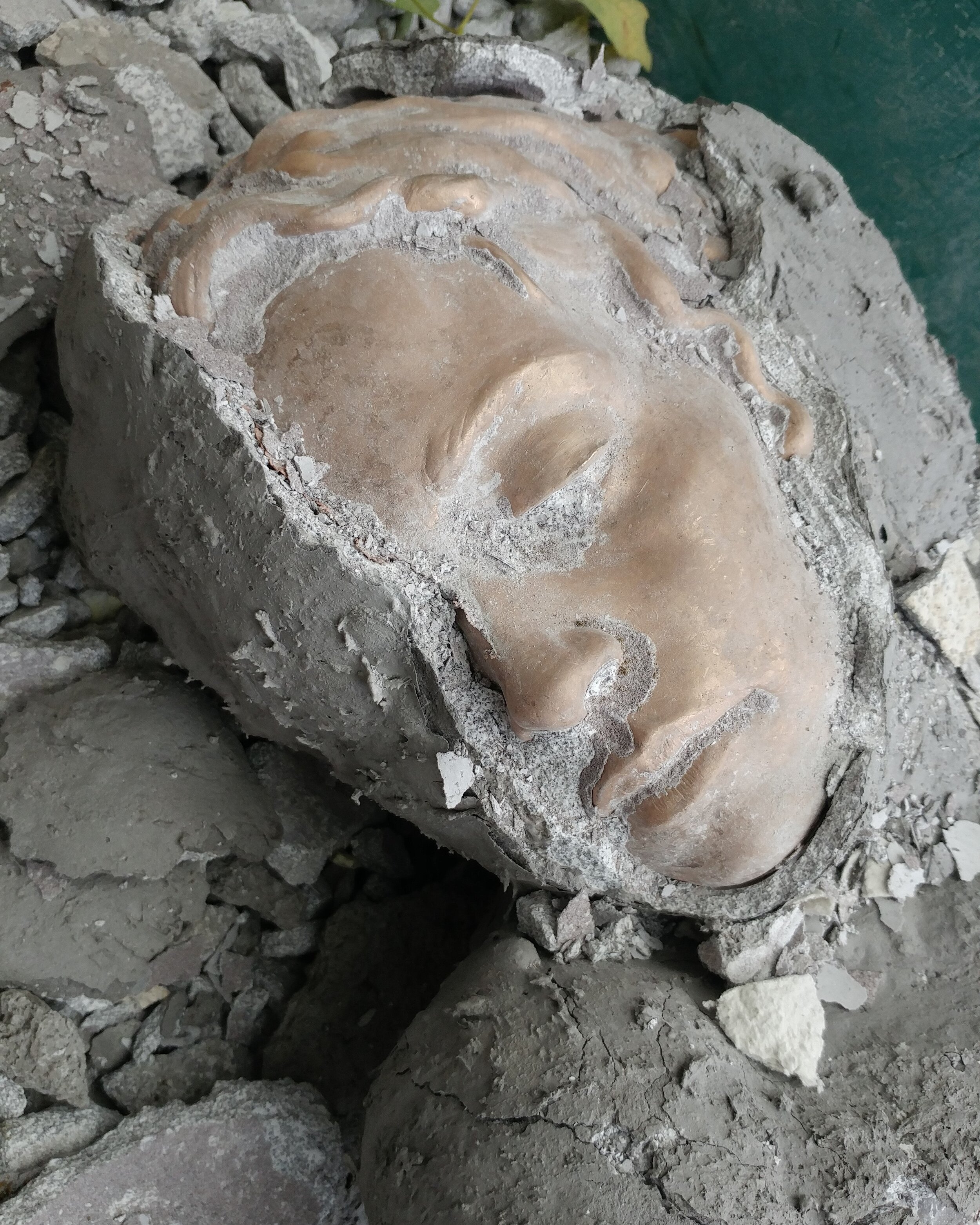
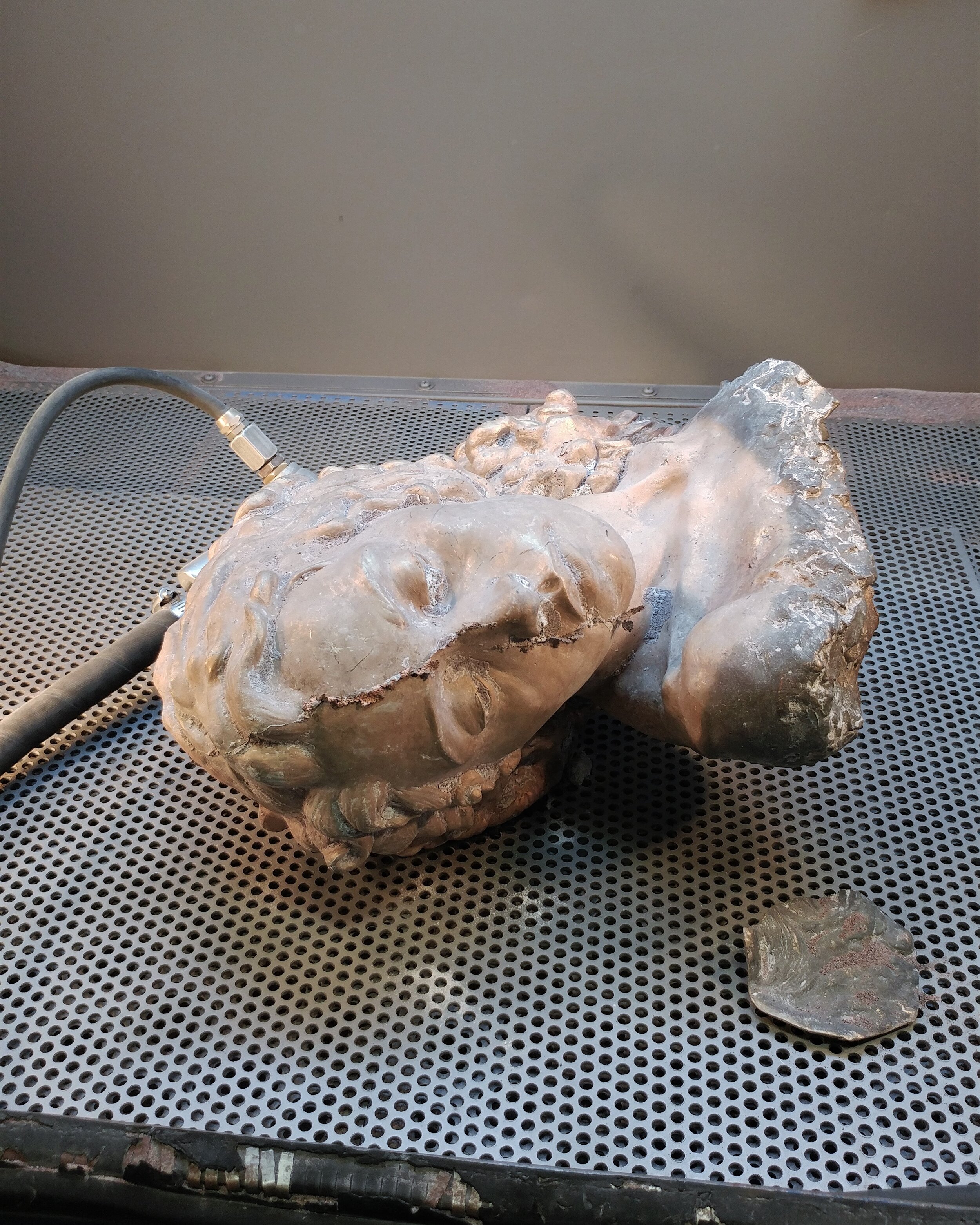
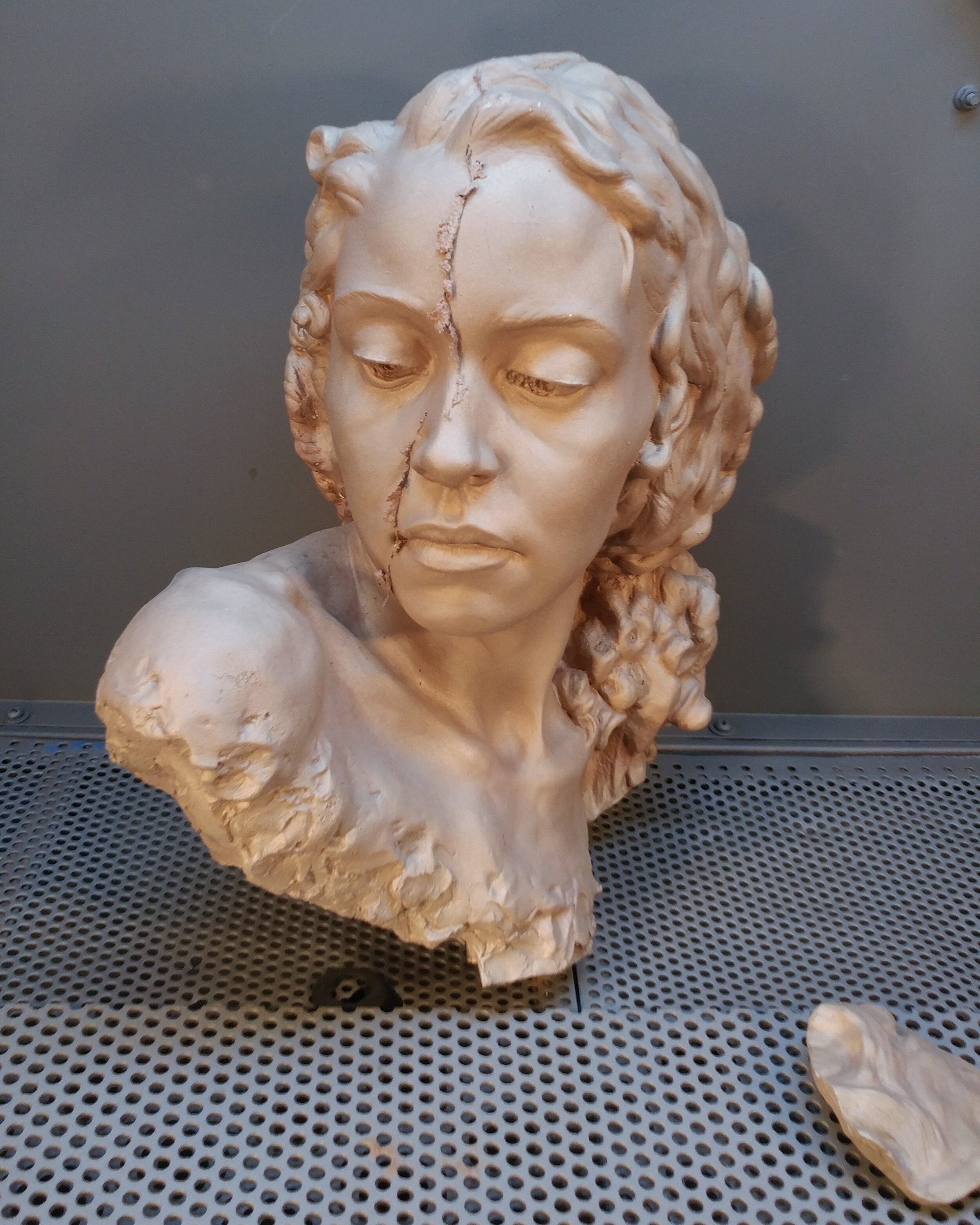
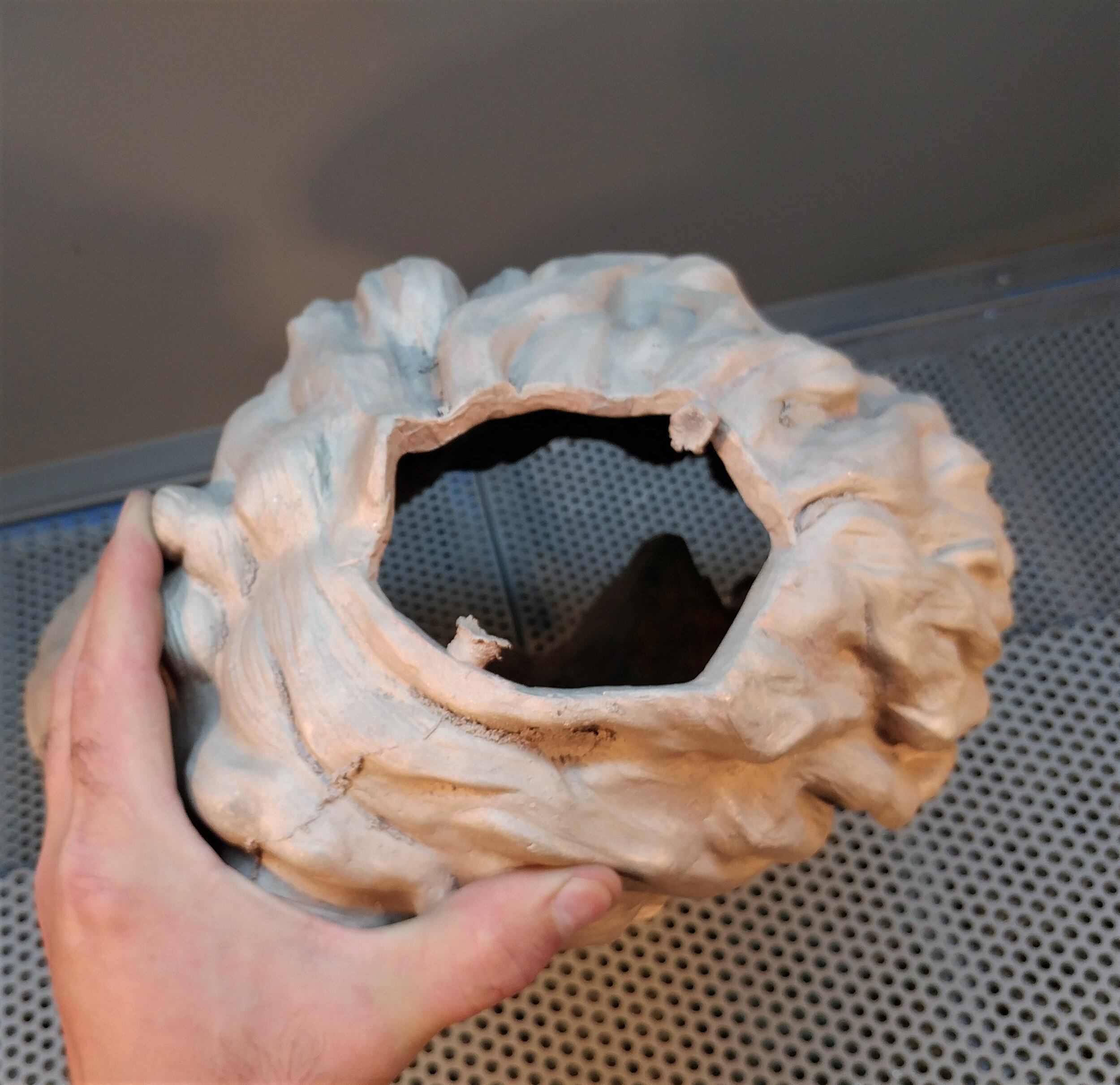
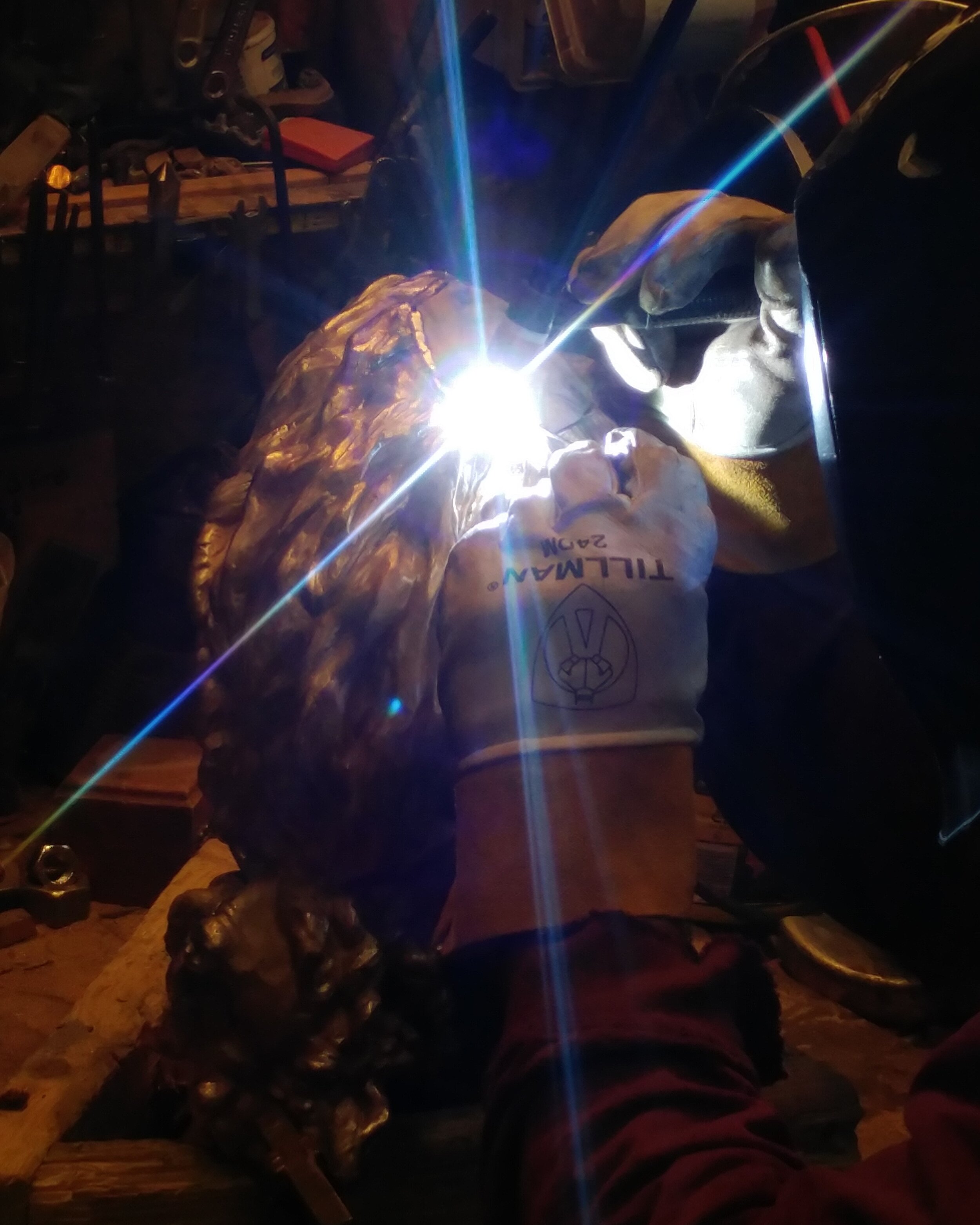
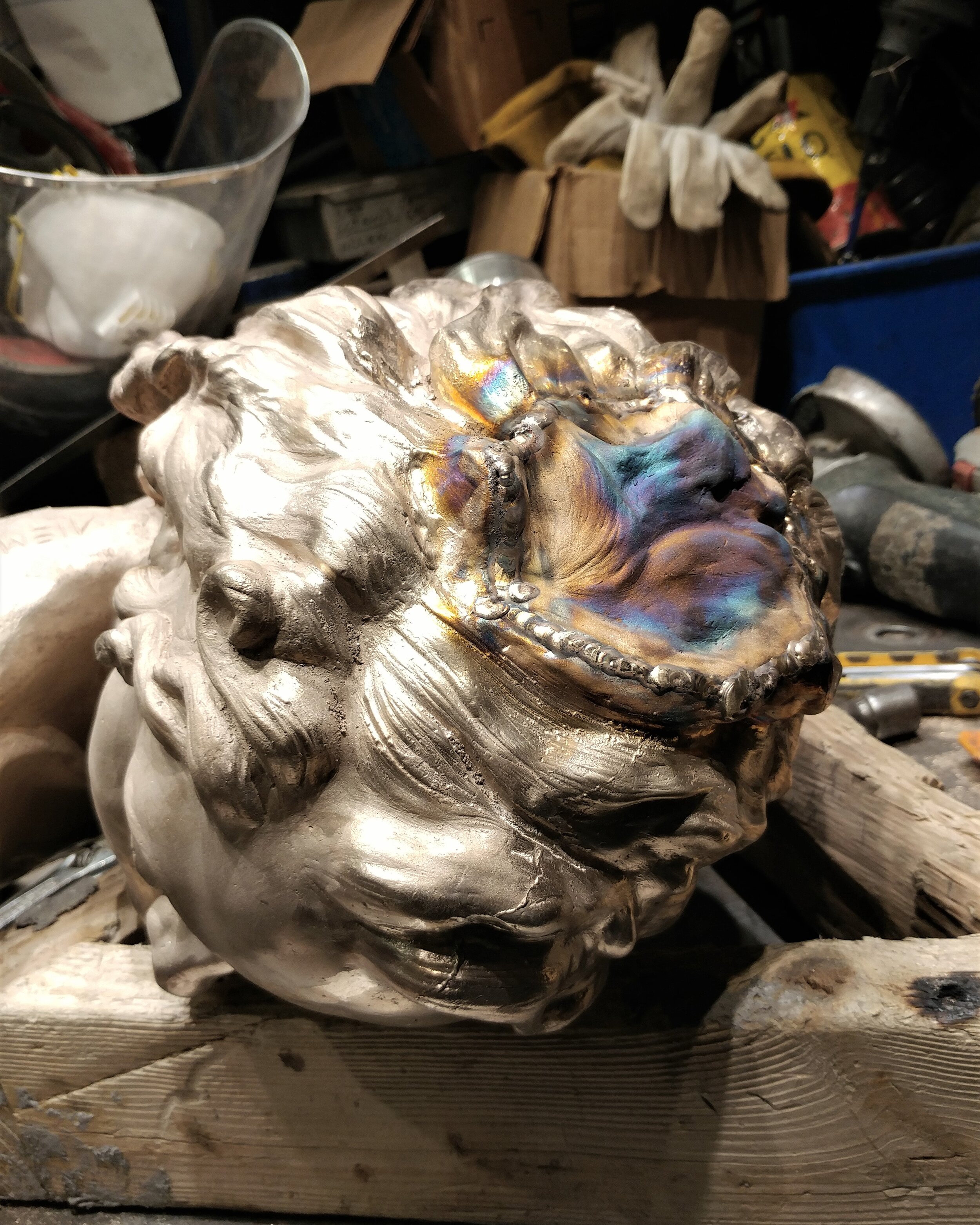
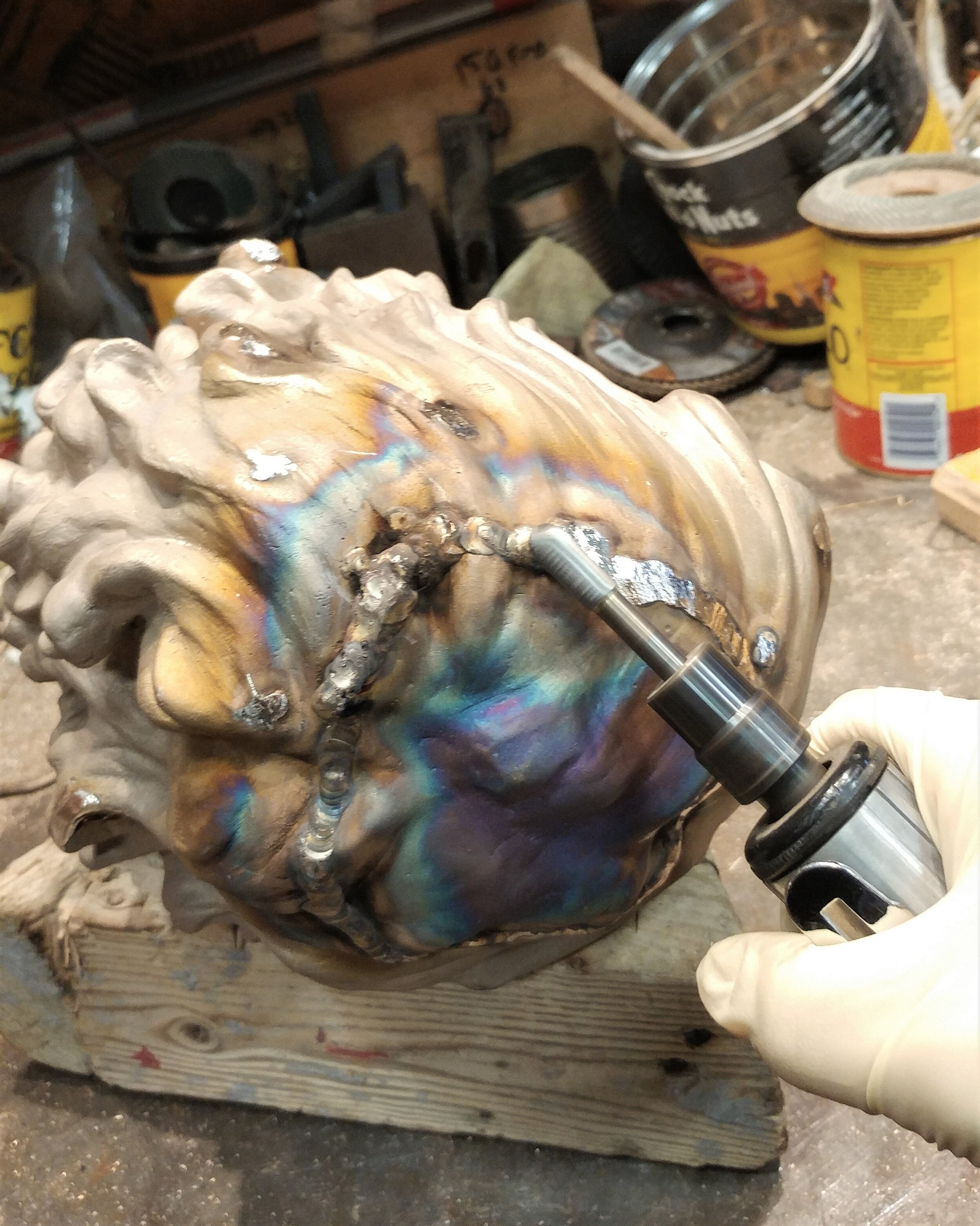
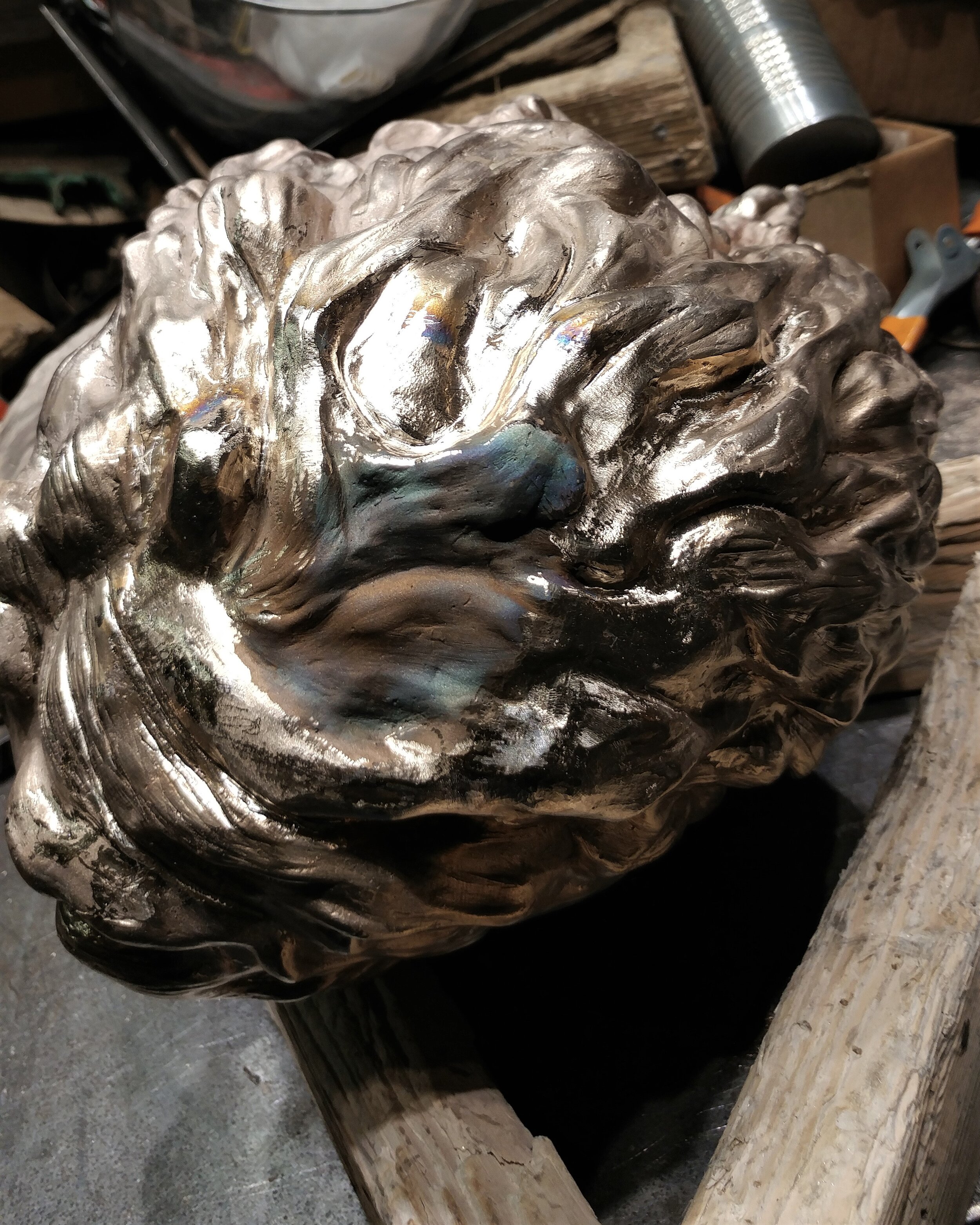
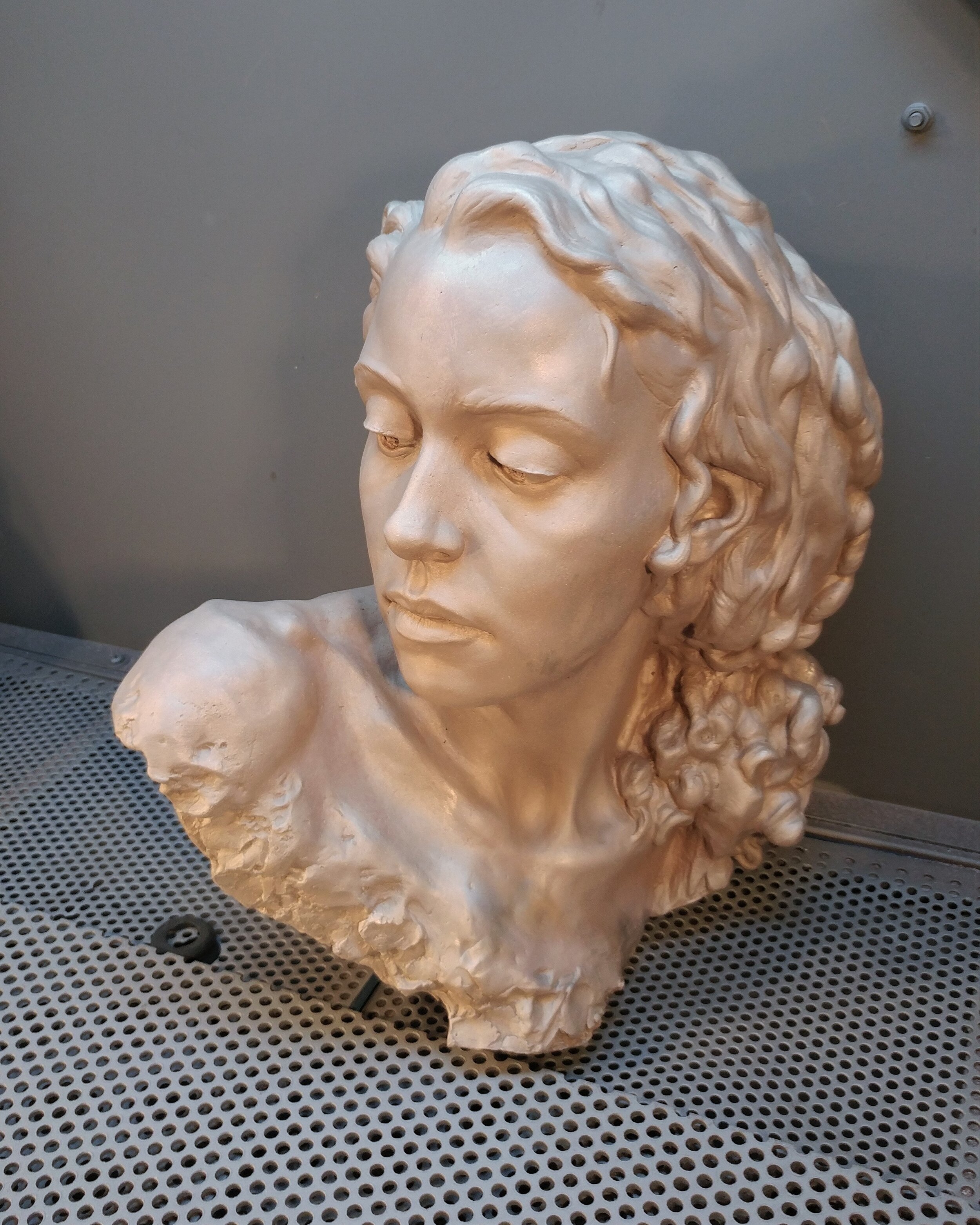
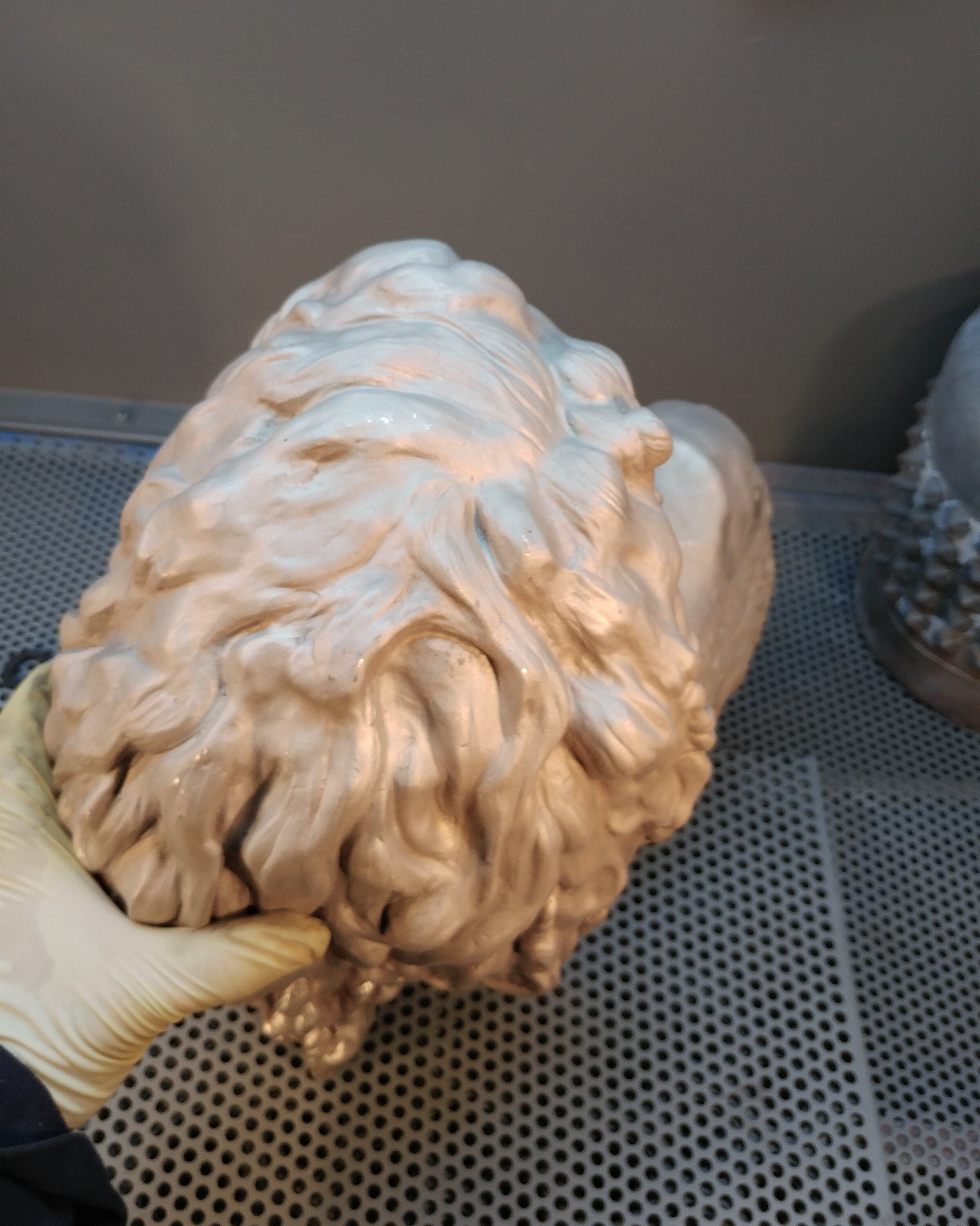
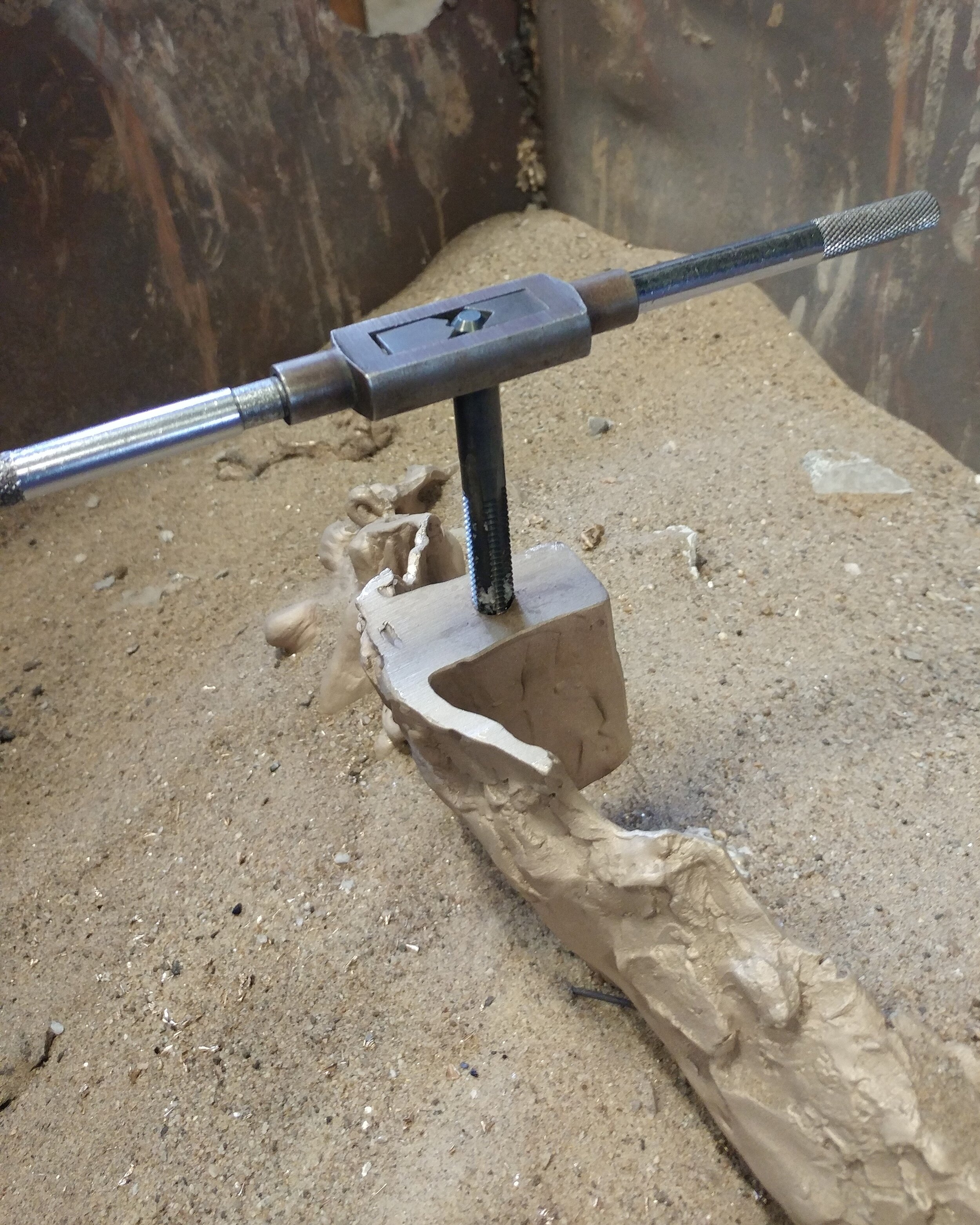
Patina
The patina is the application of a finish to the surface of the bronze. The metal has a chemical reaction to oxygen and moisture called oxidization. Oxidization produces a thin layer of rust on the surface. This can be guided to produce a variety of colors and looks depending on the chemicals used. Patination is an art in and of itself. There are a variety of finishes to choose from and the possibilities are endless. The bronze sculpture is sandblasted, then the surface is treated with heat and chemicals in a layering effect. When the desired appearance is achieved, the sculpture is sealed with a lacquer or wax to protect the Patina.
Delivery and Installation
When the sculpture is complete, it’s delivered to the client. It is either mounted to a base or permanently installed on location. The final balance is due upon delivery.